Top Compressors for Natural Gas: Applications and Benefits
The Backbone of Effective Treating of the Natural Gas
Natural gas has become one of the most essential resources in the current society as a primary source of energy for home use, industries, and transport amongst others. These elegant machines guarantee that natural gas moves efficiently within pipelines, is appropriately regulated, and is utilized for multiple purposes including gas-fired electricity generation and LNG production. The compressors for natural gas can also be understood with a quick look at their types, applications, and role in managing the energy system.
Introduction to Natural Gas Compressors
Natural gas compressors act as a means of pumping the gas from one point to another as they compress it in the process. In terms of pipeline networks or storage tanks, these machines scale down the volume of natural gas by qualifying the pressure. This process is quite effective and convenient for the transportation of gas over long distances, storage, and energy generation.
Natural Gas Compression Systems Rely on Three Critical Aspects:
• Compression ratio: It is the ratio of the initial pressure of the gas to the pressure of the same species of the gas after compression.
• Discharge pressure: The so-called delivery pressure of the gas after it has been pressurized.
• Flow rate: The amount of gas that needs to be compressed and transported or displaced altogether.
Types of Compressors for Natural Gas
It should be also noted that the classification of natural gas compressors is made according to the need of their use. All these types of compressors are designed to perform certain duties in industrial applications such as maintaining pressure in pipelines or in complex processes such as in Liquefied Natural Gas production.
Centrifugal Compressors
Centrifugal compressors are ranked as the most used type of gas compression in the industry. These machines operate by imparting velocity to the gas through the use of high-speed rotating impellers, thereby converting the kinetic energy into pressure. Basically, they are widely used in fields that require the transportation of massive amounts of gaseous media at rather low pressure.
• Applications: Especially suitable for Natural Gas Pipelines and Gas Processing Plants.
• Efficiency: Highly efficient especially for high flow applications in terms of pressure drop across the unit.
• Maintenance: Use, needs constant maintenance so that its impellers can easily crush and push out unwanted contents.
Reciprocating Compressors
These are piston-operated devices used to compress gases in tanks. A reciprocating compressor is used for high-pressure applications but they are widely used in situations that require accuracy.
• Applications: Regasification, small-scale liquefaction, and temporary storage.
• Efficiency: Best for those situations and conditions where there is much pressure.
• Reliability: More robust in construction possibly more expensive to maintain due to mechanical components.
Screw Compressors
Screw compressors utilize two meshing helical screws to compress gaseous media which are the advantages and disadvantages of helical screw compressors used in industries. They are characterized by a high level of performance and stability with space-adjustable applications.
• Applications: LNG production and their precursor gas processing plants.
• Efficiency: Relatively efficient especially in a factory where the operations are strictly ongoing.
• Safety: Safe and dependable for heavy use and for harsh conditions.
Rotary Screw Compressors
The rotary screw compressor is widely used in industries that require a constant, steady supply of compressed air. They have minimal mechanical problems as they are not complicated in design and are thus suitable for rigorous tasks.
• Applications: Ideal for utilization in the gas processing plant and in pipeline transportation.
• Efficiency: This type is consistent and reliable under continuous loads.
• Maintenance: Accepting little or no maintenance, substantially guarantees long-term effectiveness for operations.
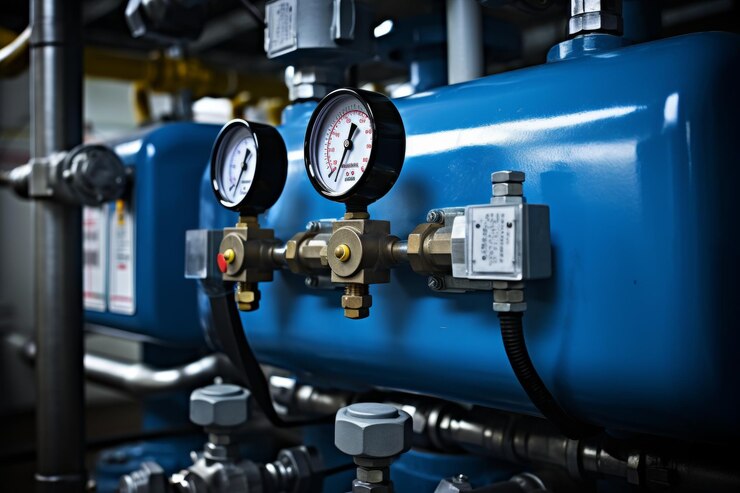
Uses of Gas Compressor
Reciprocating types of natural gas compressors are widely used in many industries as they are essential. Whether it is anything concerning the transportation of gases through pipelines or the process of converting them to other forms, these are some of the most vital components of energy.
Natural Gas Pipelines
• Key Role: Compressors ensure that the gas is always at the desired pressure.
• Technology: Piston and centrifugal compressors can be said to be the most suitable for use in the pipeline compressor.
Gas Processing Plants
• Key Role: Compressors are useful in refining as well as treatment of the gasses required for market purposes.
• Efficiency: In order to meet plant specifications and regulatory requirements highly efficient compression is applicable.
Gas Storage Facilities
• Key Role: Compressors hold gas under higher pressure in storage facilities which are mostly placed underground.
• Safety: Stable and secure compressors are very important so as to prevent leakage of the gas during storage moments.
LNG (Liquefied Natural Gas ) Production
• Key Role: The liquefaction process requires the use of compressors in order to function efficiently.
• Technology: While screw and reciprocating are usually preferred for high pressures.
What Do You Need to Know When Selecting a Compressor?
The experts have noted that in the choice of compressor for natural gas, there are various technical considerations. These factors assist in deciding which sort of compressor is most appropriate for certain applications.
Compression Ratio
The most important is the compression ratio because its value defines the gas pressure that will be raised more often. Processes, that involve highly pressurized gasses, like, storage and LNG production, require a higher compression ratio in the compressors.
Discharge Pressure
Discharge pressure simply relates to the pressure of the gas at the end of the work the compressor has done. Each application has a predetermined requirement for the discharge pressure ranging from pipelines to gas processing plants.
Flow Rate
Flow rate determines the effectiveness of the compressor in carrying gas. Like in the pipeline and LNG industry, a higher value of flow rate is necessary in order to achieve competitive productivity of the compression equipment.
Efficiency
When it comes to operation costs, it is of paramount importance to recognize energy efficiency as one of the key agendas. Energy-efficient compressors mean less energy is used to compress the gas which translates to lower fuel bills.
Reliability
These compressors are in critical application areas, and subsequently, reliability is typically very important. The stability of materials with high levels of durability, maintenance, and most of all, the appropriate technological features used have crucial roles to play in making sure that a certain facility can withstand long-lasting uses.
Maintenance
Compressors require frequent care to sustain operational efficiency. It is important to realize that various types of compressor are serviced differently and will require different types of maintenance; for instance, reciprocating compressors will require more frequent check-ups than will centrifugal compressors.
Safety Considerations in Gas Compression
Gas compression is a process that must be handled with care, given the potential hazards associated with high-pressure natural gas. Modern compressors are equipped with numerous safety features to mitigate risks, including:
• Gas leak detection systems to ensure no leaks occur during compression.
• Pressure regulation technologies to prevent over-pressurization.
• Advanced monitoring systems to provide real-time data and alerts in case of mechanical issues.
Conclusion:
Compressors for natural gas are a vital part of our energy infrastructure. From pipelines to LNG production, they play a crucial role in ensuring that natural gas is transported, processed, and stored efficiently and safely. Understanding the different types of compressors, their applications, and the technical details involved can help you make informed decisions on which equipment best suits your needs. To explore more about natural gas compressors and related products, visit our natural gas compressor solutions.