The Ultimate Guide to Fuel Gas Boosting Screw Compressors (2024)
Gas turbine power plants are the mainstay of modern electricity generation – offering secure and flexible energy provision. Gas turbines ramp up and down in minutes compared to the hours necessary for coal or nuclear plants, ensuring gas fills the gaps as renewable energy generation waxes and wanes throughout a typical day. This is achieved by burning fuels such as natural gas, which heats air at high pressure and spins turbines to create electricity. Together with power generation, however efficiency matters. That is where Fuel Gas Boosting Screw Compressor comes in.
The Need for Fuel Gas Boosting Screw Compressor
A ground-based jet engine primed to pump out electricity. This is a gas turbine power plant, essentially. The job of this engine is to breathe in air and pump it up to high pressure hot enough that it explodes when mixed with fuel into a combustible gas stream.
This gas turns the turbine to produce electricity. Just like the engine in a car requires an optimal amount of fuel to run correctly, gas turbines require more precise values for their requirements on entry average temperature and when changing over from one operation state to another.
High fuel gas pressure is one requirement that can not fail. This high pressure assists in the efficient operation of the turbine. The stream is the water and it rates of flow are analogous to how fast we can squeeze that hose (ie a high-pressure hose = faster rate). Likewise, greater fuel gas pressure allows the turbine to more efficiently consume that fuel and extract as much energy from it.
Performance and Efficiency
What happens, when gas expansion drives gas turbines do not receive fuel gas at the correct pressure? The most straightforward fallout of the system being offline is a loss in both efficiency and power.
Efficiency means how well the power plant turns fuel into electricity. When the fuel gas pressure drops, less energy is released for the turbine to burn completely and it’s more wasted combustion And also higher Fuel Consumption. This means the power plant has to spend more money for operation.
Finally, in summary, low fuel gas pressure is a significant cause of poor performance for this Gas turbine and it cannot be ignored. This is where fuel gas boosting technology will help us, as it ensures these power plants operate in an efficient way to generate more electricity and fewer CO2 emissions by the use of low-quality fuels which would result from a cleaner electric grid.
Challenges of Fuel Gas Boosting Screw Compressor
Suction Gas Pressure Fluctuation
Like hitting the gas pedal in a car, that instant spike is akin to demand jumping up inside of your power plant. The fluctuations in these gas pressures may result from variability in the load on the turbine. It is difficult for the compressor, resulting in more work needing to be done by it so that high pressure of a constant level can be passed on into the turbine and needs to be compensated again.
Oil Carryover and Pulsation/Vibration
While other compressors use oil lubrication. That cuts both ways, and this can be good as much as it could earn. The oil, which both bathes and lubricates internal engine components to keep them spinning with minimal resistance, is also easily vaporized into the gas stream (oil carryover).
This oil gas can cause problems in the future. First, it may reduce the power output of the turbine – such as having fouled spark plugs in your car. Furthermore, the oil can result in more frequent maintenance and repair due to accelerated wear on vulnerable turbine elements.
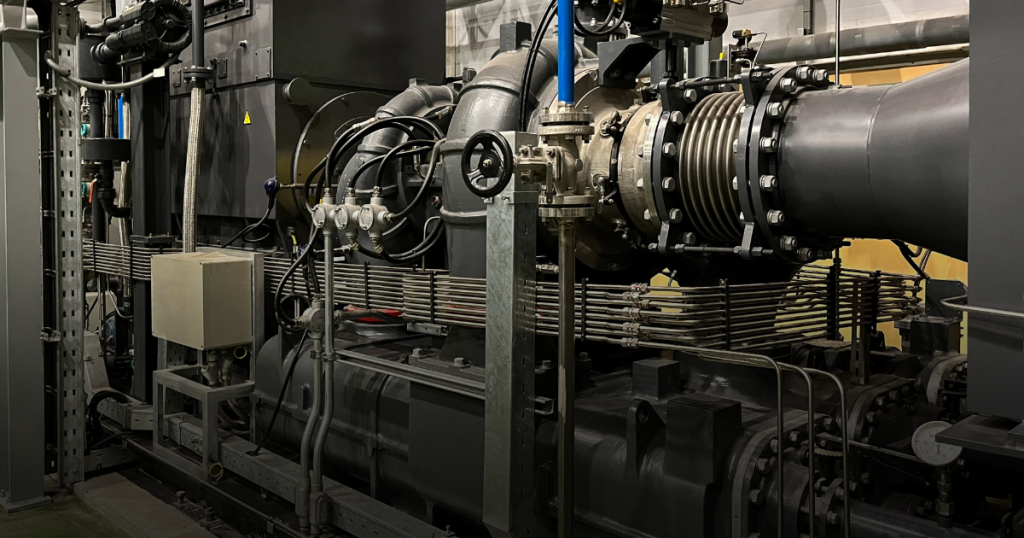
Fuel Gas Boosting Screw Compressor Designs for Boosting Applications
It is not the case always that natural gas has pressure to be utilizable One of the elements that prevents the gas from being more widely used is how bulky and liquid it becomes under pressure – cue fuel gas compressors!
These engines can pressurize low-pressure gas to higher pressure so it can be used for tasks such as fueling turbines that generate electricity. Then which is the best compressor with different designs available? Cutting it short, main three types:
Centrifugal compressors:
Like a fan, running fast. Or in the case of a centrifugal compressor(OP), that is the simple working. It employs rotating blades to give rise to gas pressure. Perfect for huge flows, but the pressure rise is not as great
Reciprocating compressors:
Imagine a piston moving up and down inside a barrel full of fluid. Is what is usually meant by a reciprocating compressor. Excellent in high pressure, but more bulky and harder to maintain.
Screw compressors:
Intermeshing screws are used to compress the gas. They strike a fine balance between pressure and flow, which eventually makes them an ergonomic choice.
What Makes High-Pressure Fuel Gas Boosting Screw Compressor Unique?
High-pressure screw compressors are rising in popularity for fuel gas-boosting applications. Here’s why:
More Power: Screw compressors can use a much higher compression ratio compared to a centrifugal compressor. That means being able to take gas at a much lower pressure and increase it to the requisite level for turbines.
Adaptability is Key: Gas Demand Variability Adaptation Turndown Ranges for High-pressure Screw Compressors This allows them to respond quickly to flow rate changes without loss of performance.
Built to Last: Fuel Gas Boosting Screw Compressor are designed to be of high strength. It has fewer moving parts than reciprocating compressors, hence having more mechanical reliability and also cutting down maintenance-related downtime.
Optimizing Screw Compressor Performance for Fuel Gas Boosting
Screw compressors are the workhorses behind efficiently delivering fuel gas to power plants. But with great power comes responsibility – both to the environment and your bottom line. Let’s explore how to optimize screw compressor performance for fuel gas boosting, keeping both factors in mind.
Environmental Considerations
Screw Compressors make significant noise This may be disturbing to others who live nearby and adds to the noise pollution. No worries, however, there are answers. Screw compressors are available with sound enclosures and mufflers to dramatically lower the noise level. Good sound-transmission reduction techniques such as mounting the compressor on vibration isolators can help reduce noise further.
Power Savings and Efficiency
One of the most important tools to help achieve this overall efficiency is a well-designed screw compressor for the power plant. Their design also incorporates features such as optimized rotor profiles and improved lubrication systems to reduce internal energy losses, rendering modern screw compressors. In short, this means less power is lost in waste and greater overall fuel efficiency for the plant.
Here’s the catch, however: The fuel gas can also impact efficiency. The following table shows the average composition of natural gas, not including water. A well-designed screw compressor gearbox can accommodate these minor variations and will still produce optimal performance while the gas composition varies.
This will allow you to run screw compressors that are more environmentally friendly, emit less noise but could even save some money in power costs – a win-win situation.
How Oil-injected Screw Compressors Boost Fuel Gas?
Think of having to push extra fuel on a high-power engine. That gas compressor is akin to a fuel gas boosting compressor in industrial applications, only much taller. These beasts all use one type of compressor specifically- the oil-injected screw compressor. Something is seriously working with them so let us get into it.
But we want no oil in the end product of hydrogen. That’s where the oil separation system comes in. A kind of super filter, carefully filtering nearly all the oil in the hydrogen stream. This in turn keeps our fuel gas clean and protects precious downstream equipment. Beneath the surface, these compressors feature a pair of intermeshing screws that squeeze hydrogen gas into higher pressures with fine tolerances.
However, friction was a relentless foe that wore down the screws. This is where lubricant oil plays a hero and keeps the screws safe by forming a thin layer. This oil is necessary to reduce power loss, friction and duration of the life at a compressor.
Oil Separation System
However, we do not want to include oil in the end hydrogen product since it can damage downstream equipment. This is where an oil separation system comes into play. A proverbial high-tech sieve that sifts out virtually every last wisp of oil the minute these oils flow from a production vessel into pressurized hydrogen trains.
Typical oil mist eliminators consist of a series of separation stages utilizing centrifugal force and filtration, to remove oil down to less than 1 part per million (ppm). This helps in keeping our fuel gas free from impurities, which also safeguards sensitive equipment downstream.
Summary
And lastly, just picture a volume knob for the compressor output. Slide valve to the rescue. With a change in its placement, the volume of hydrogen provided by the compressor can be manipulated. This provides exceptional accuracy in the control of the pressure and flow rate of fuel gas, ensuring that it performs at its best for your application. If you are looking for High Quality Fuel Gas Boosting Screw Compressor then Explore Fuel Gas Boosting Screw Compressor.
Read more: Recip Compressor Services Ltd: Keeping Your Industrial Heartbeat Strong