Synthesis Gas Compressors: Driving Efficiency in Modern Gasification and Chemical Processes
In the ever-evolving world of energy and chemical manufacturing, synthesis gas (syngas) has become a key component in the production of cleaner fuels, chemicals, and even hydrogen. At the heart of syngas production lies a vital piece of equipment: the synthesis gas compressor. This critical machinery plays an essential role in compressing gas streams that are often a complex mixture of hydrogen (H₂), carbon monoxide (CO), carbon dioxide (CO₂), and other trace gases. As demand for clean and sustainable energy increases, understanding the function, applications, and technological advancements of synthesis gas compressors is key to optimizing syngas-based processes.
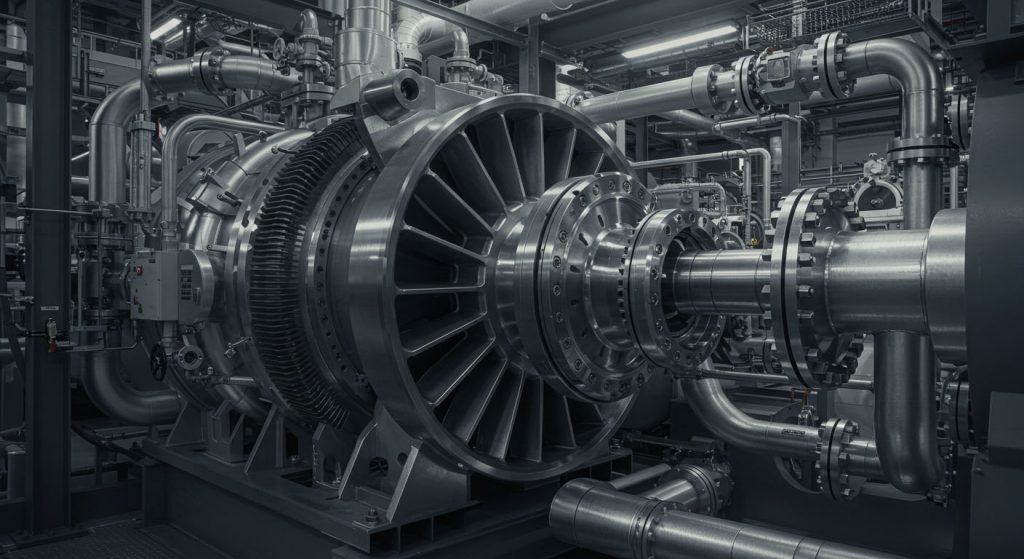
What is Synthesis Gas?
Synthesis gas, or syngas, is primarily composed of hydrogen and carbon monoxide. It is produced from various feedstocks like coal, biomass, or natural gas through processes such as gasification or steam methane reforming (SMR). Syngas serves as a building block for the production of synthetic fuels, chemicals like ammonia and methanol, and even hydrogen for fuel cells.
However, handling synthesis gas presents challenges due to its high pressure, complex composition, and volatile nature. This is where synthesis gas compressors come in.
Why Synthesis Gas Compressors are Essential
Synthesis gas compressors are designed to handle the pressure and flow variations associated with syngas production. Whether you’re working with syngas in a power plant, chemical production facility, or hydrogen generation plant, compressing the gas efficiently is crucial for ensuring both energy efficiency and safety. Here are the key reasons why synthesis gas compressors are indispensable:
- High Pressure Handling: Syngas is typically produced under high pressure, and compressors are needed to maintain and manage these pressures effectively throughout the system.
- Complex Gas Mixture: Synthesis gas often contains varying ratios of H₂, CO, CO₂, and other trace gases, requiring compressors capable of safely handling such complex mixtures.
- Energy Efficiency: Compressing syngas demands energy, so highly efficient compressors are needed to ensure minimal operational costs and reduced environmental impact.
- Safety Considerations: Due to the flammable and sometimes toxic nature of syngas, compressors must be designed with stringent safety standards to avoid leaks or explosions.
Key Applications of Synthesis Gas Compressors
Synthesis gas compressors are widely used in industries such as energy, chemicals, and manufacturing. Some of the key applications include:
1. Power Generation and Carbon Capture
In integrated gasification combined cycle (IGCC) power plants, syngas is generated from coal or biomass and used to produce electricity. Compressors are crucial to maintain syngas pressure before it enters the turbine. Moreover, syngas compressors are critical for capturing and processing CO₂ from power generation, helping reduce greenhouse gas emissions.
2. Hydrogen Production
Syngas is a vital intermediate in hydrogen production via processes like steam methane reforming (SMR). Compressing the syngas allows for efficient conversion into hydrogen, a crucial fuel for clean energy applications, such as fuel cells and industrial processes.
3. Chemical Synthesis
Syngas serves as a feedstock for producing various chemicals, including methanol, ammonia, and synthetic fuels. Synthesis gas compressors are used to compress the gas to the required pressures for these chemical processes, ensuring the production of high-quality end products.
4. Biomass Gasification
Biomass gasification is a renewable method of producing syngas from organic material. Synthesis gas compressors are an integral part of converting biomass into valuable fuels and chemicals, enhancing the efficiency of the entire gasification process.
Technological Advancements in Synthesis Gas Compressors
As industries move toward more sustainable practices, synthesis gas compressors have undergone several technological advancements to improve efficiency, safety, and performance. Here are some key innovations:
1. Oil-Free Compression
Modern synthesis gas compressors often feature oil-free designs, which are essential for preventing contamination of the syngas. This is particularly important when the syngas is used for high-purity applications like hydrogen production.
2. Energy-Efficient Motors
With increasing energy costs, the need for energy-efficient motors in compressors is more pronounced than ever. Variable frequency drives (VFDs) are now commonly integrated to adjust the compressor speed based on demand, significantly reducing energy consumption.
3. Corrosion-Resistant Materials
Syngas typically contains trace amounts of corrosive elements, such as hydrogen sulfide (H₂S). Compressors are now being manufactured with corrosion-resistant materials to improve their lifespan and reliability in harsh operating conditions.
4. Smart Monitoring and Automation
The integration of IoT-based monitoring and automation systems in compressors allows for real-time performance tracking. Predictive maintenance features help reduce downtime and optimize compressor efficiency by identifying potential issues before they occur.
Conclusion
Synthesis gas compressors are critical components in the gasification, chemical production, and hydrogen generation industries. As syngas continues to play an integral role in the global energy transition and chemical production, the demand for efficient, safe, and reliable compressors is set to rise. At LEiYAO Compressors, we provide cutting-edge solutions that help industries harness the full potential of syngas, ensuring operational excellence and contributing to a sustainable future.
By choosing the right synthesis gas compressor, businesses can ensure that their syngas systems operate at peak performance while minimizing energy consumption and maintaining the highest safety standards.