Save Money & Energy: Why Choose a 3 Stage Gas Compressor
The Powerhouse of Industrial Gas Movement: A Comprehensive Guide to 3 Stage Gas Compressors
The effective flow of gases is essential to the industrial world’s survival. The 3 stage gas compressor is the vital workhorse at the centre of this operation. This technical marvel rises to the task of producing high-pressure gas output, which makes it a crucial part of many industrial applications.
This in-depth manual explores the realm of these compressors and equips you with extensive information. We’ll go over their features, uses, advantages, and important selection factors. This essay provides insightful information for everyone interested in industrial processes, regardless of expertise level as an engineer.
Demystifying the 3 Stage Gas Compressor: A Multi-Stage Approach to High Pressure
These compressors have a three-phase compression operation, in contrast to its single-stage equivalent. This is an explanation of how it functions:
- Intake and First Compression:
Low-pressure gas is drawn into the compressor’s first stage upon entering. Here, the gas is compressed by rotors or pistons to a moderate pressure.
- Intercooling:
As a result of the first compression, the gas warms up. Next, a heat exchanger called an intercooler is used to channel the hot gas. By lowering the gas’s temperature, this intercooler increases efficiency and guards against overheating in later phases.
- Second and Third Stages of Compression:
After cooling down, the gas moves on to the second stage, where it is compressed even more, increasing in pressure from the first. In the third stage, this procedure is repeated to produce the final high-pressure output that is needed.
- After cooling and Discharge:
The gas goes via the aftercooler, which is an additional heat exchanger, following the last compression step. This guarantees that the compressed gas reaches the right temperature for the purpose for which it is intended. The high-pressure gas is then released from the compressor and used for the purpose for which it was designed.
The Heartbeat of Power: Key Components of a 3 Stage Gas Compressor
It is an elaborate ensemble of elements that operate together harmoniously rather than just one unit. Each part is essential to producing the high-pressure gas production needed to power different industrial operations. Let’s examine the essential components of this behemoth as we go inside:
Chambers of compression:
- Cylinders (Reciprocating Compressors):
The pistons that compress the gas at each stage are housed in cylinders, often known as reciprocating compressors. The pistons’ up-and-down motion raises the gas pressure.
- Rotors (Screw Compressors):
As they revolve, intermeshing rotors inside the casing capture and compress the gas. Constant compression is possible because of the architecture.
The Driving Force:
- The reciprocating action of the pistons is converted into rotary motion by the crankshaft, which is an essential component of reciprocating compressors. It transmits power to compress the gas through a connection to the driver.
Controlling the Flow
- Intake and Discharge Valves:
These valves regulate the flow of gas into and out of each compression stage by acting as gatekeepers. Effective gas transport is ensured by precise timing.
Staying Calm Under Duress:
- Intercoolers and Aftercoolers:
The heroes of a three-stage compressor are the intercoolers and aftercoolers, which are heat exchangers. The gas heats up after each stage of compression. As radiators, intercoolers and aftercoolers lower the gas temperature in between stages. By doing this, overall efficiency is increased and overheating in later compression stages is avoided.
Keeping Things Smooth:
- Lubrication System:
Efficiency is hampered by friction. By reducing friction between the moving parts of the compressor, a well-designed lubrication system guarantees smooth operation.
The Source of Power:
- Driver (Electric Motor or Engine):
The driver, which can be either an electric motor or an engine, is the part that powers the whole thing. The power needed to run the compressor and provide the requisite pressure output comes from internal combustion engines or electric motors.
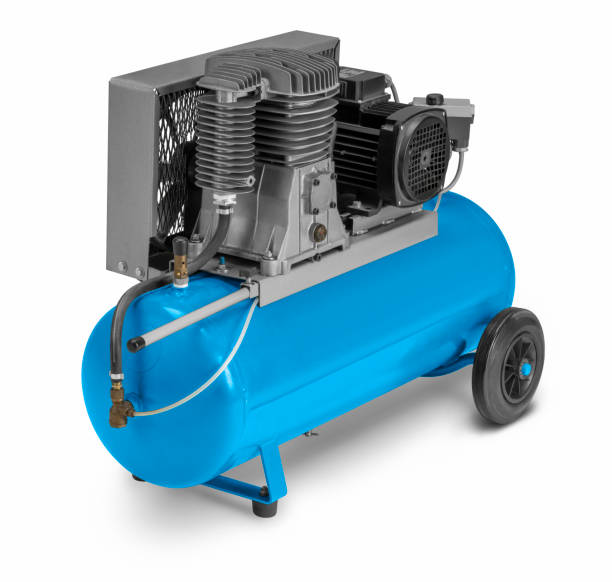
Revealing the Uses for Three-Stage Gas Compressors: An Unimaginable World
3 stage gas compressor is capable of far more power than first appears. These industrial workhorses’ power vital operations in many different sectors and play a crucial role in a surprisingly wide number of applications. Let’s set out to explore the hidden world where three-stage gas compressors rule supremely:
The Source of All Energy:
- Natural Gas Transportation:
Three stage compressors are used to move this essential fuel over vast distances in an effective manner by high-pressure pipelines that supply natural gas to your residence or place of business.
The Building Blocks of Industry:
- Air Separation Units (ASUs):
These specialized facilities are necessary for a variety of industrial processes because they can separate atmospheric air into its parts, such as oxygen, nitrogen, and argon. The key to reaching the high pressures required for this separation is three-stage compressors.
- Chemical Processing:
Precise pressure control is advantageous for a variety of chemical reactions. This control is provided by three-stage compressors, which provide ideal circumstances for a range of chemical processes.
Keeping it Cool:
- Refrigeration Systems:
They are used in industrial refrigeration systems, which preserve food and carry out other temperature-controlled operations, to reach the low temperatures necessary for effective operation.
From Unusable to Useful:
- Petrochemical Industry:
These gas compressors play a crucial role in pressure control procedures all along the production chain, from the refinement of crude oil to the creation of different petrochemical products like plastics and fertilizers.
Energizing the Future
- CNG (Compressed Natural Gas) Fuelling Stations:
To provide cleaner and more environmentally friendly transportation options, natural gas must be compressed to a proper pressure using three-stage compressors.
Fuelling the Abysses:
- Oil and Gas Production:
These compressors help with several areas of the industry, such as pipeline gas transportation, well pressure enhancement during extraction, and natural gas reinjection back into reservoirs.
Embracing the Advantages: Why Choose a 3 Stage Gas Compressor?
The compressor that is selected is important in the high-pressure realm of industrial gas flow. While single-stage compressors are useful in some situations, 3 stage gas compressor is the undisputed leaders in situations where outstanding performance is required. This is the reason why:
- Overcoming Mountains of Pressure:
The capacity of these compressors to attain noticeably higher discharge pressures than single-stage ones is their key benefit. They can handle challenging applications requiring gases compressed to remarkable levels because of their multi-stage method.
- Efficiency Leading the Way:
The intercoolers are the key ingredient. Three-stage compressors lessen the amount of effort needed in later stages by deliberately chilling the gas in between compression stages. As a result, they become more efficient and can produce greater pressure outputs with less energy usage. This results in financial savings as well as a smaller environmental impact.
- Dependability You May Trust:
These gas compressors are incredibly reliable due to their sturdy construction and multi-step compression method. These workhorses minimize downtime and maintenance costs with longer lifespans and dependable operation due to less strain on each compression stage.
- Designed to Meet Your Needs:
3 stage gas compressor is available in a range of configurations to suit various needs. There’s a three-stage compressor model that’s ideal for your particular requirements, regardless of the flow rates or pressure ranges you need. This degree of adaptability guarantees that you will be able to locate the best answer for your particular industrial procedure.
- A Sustainable Option
These compressors use less energy because of their increased efficiency. This minimizes your environmental effect and lowers running expenses while also promoting a more sustainable future.
Safety First: Crucial Considerations When Operating a 3-Stage Gas Compressor
It is an industrial workhorse due to its enormous capacity, but great power also comes with considerable responsibility. Safety must always come first when using this equipment. To guarantee a secure and seamless operation, take into account these crucial factors:
Power comes from Knowledge:
- Examine and comprehend the user’s manual:
Important details about the particular model you’re using, such as operating guidelines, maintenance schedules, and safety measures, are included in this handbook.
- Training is essential:
Make the most of any operator training provided by your employer for 3-stage gas compressors! Accident risk is reduced by following the right procedures.
The Importance of Personal Protective Equipment (PPE)
- Safety glasses:
Wear safety glasses to protect your eyes from flying debris and possible spills of liquid.
- Protect your hearing:
These compressors are very noisy. To preserve your hearing, put on earmuffs or earplugs.
- Safety footwear:
Robust boots featuring steel toes shield your feet from potential falls or dropped objects.
Use Caution When Operating:
- Never apply more pressure or capacity than is rated:
Excessive use of the compressor may result in catastrophic failure.
- Keep a safe distance from them:
When the compressor is running, stay away from it.
- Watch out for heated surfaces:
During operation, parts like the discharge piping and cylinders can get extremely hot. Keep your hands off of them.
Conclusion:
LIEYAO Compressor stands out as a dependable partner for your industrial demands when it comes to 3 Stage Gas Compressor. We build our compressors with an unrelenting dedication to longevity, performance, and efficiency. Our gas compressors are designed to provide outstanding performance in demanding applications such as chemical processing, natural gas transportation, or any other situation where high-pressure output is needed. Discover the distinction and take your operations to new levels.