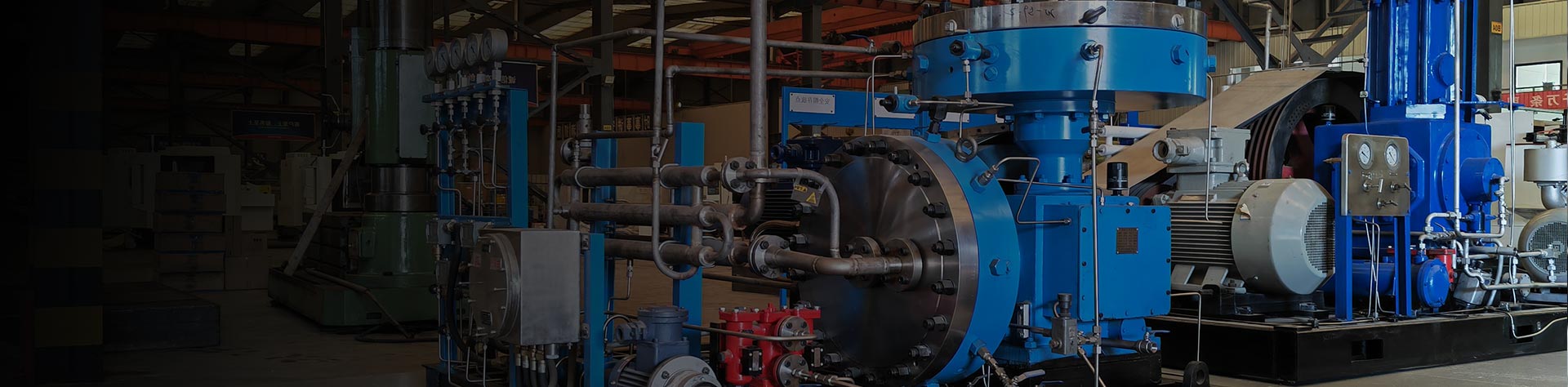
Reciprocating Compressor
A reciprocating compressor is a type of positive displacement compressor that uses a piston-cylinder mechanism to compress gas. This compressor operates through a reciprocating motion of a piston within a cylinder, creating a suction stroke to draw in gas and a compression stroke to reduce the volume of the gas, thereby increasing its pressure.
A reciprocating compressor, also known as a piston compressor, is a type of positive displacement compressor commonly used in various industries. It works by drawing in a volume of gas, compressing it through a reciprocating motion of a piston within a cylinder, and then discharging it at a higher pressure. Here are some key aspects of reciprocating compressors:
- Operation Principle: The basic mechanism involves a piston moving back and forth in a cylinder. As the piston moves down, it creates a vacuum that draws in gas through an intake valve. When the piston moves up, the gas is compressed and then discharged through an outlet valve.
- Single-Stage and Multi-Stage: Reciprocating compressors can be single-stage or multi-stage. In a single-stage compressor, the gas is compressed once; in a multi-stage compressor, the gas undergoes several stages of compression, which improves efficiency and can achieve higher pressures.
- Cooling System: Due to the heat generated during compression, these compressors often come with cooling systems, which can be air-cooled or water-cooled.
- Applications: Reciprocating compressors are widely used in various applications, including refrigeration, air conditioning systems, gas pipelines, oil refineries, chemical plants, and natural gas processing plants.
- Efficiency: They are known for their efficiency in high-pressure applications and can be designed to handle a wide range of gases.
- Maintenance: Reciprocating compressors require regular maintenance, including lubrication, valve checks, and replacement of wear parts like piston rings and bearings.
- Durability: They are generally robust and can have a long operational life if properly maintained.
- Noise and Vibration: One drawback of reciprocating compressors is that they tend to generate more noise and vibration compared to other types of compressors, like screw or centrifugal compressors.
Features & Characteristics:
Here are some key features and components associated with reciprocating compressors:
- Piston and Cylinder Assembly: The reciprocating motion is achieved by a piston moving back and forth within a cylinder. During the suction stroke, the piston moves away from the cylinder head, creating a vacuum and allowing gas to enter. In the compression stroke, the piston moves towards the cylinder head, compressing the gas.
- Crankshaft and Connecting Rod: The piston is connected to a crankshaft through a connecting rod. The crankshaft converts the rotary motion into a reciprocating motion, facilitating the up-and-down movement of the piston.
- Valves: Reciprocating compressors typically have two types of valves: suction (inlet) valves and discharge (outlet) valves. These valves open and close to control the flow of gas into and out of the cylinder.
- Cylinder Head: The cylinder head houses the valves and provides a sealed enclosure for the compression process. It also contains passages for cooling and lubrication.
- Motor or Engine: Reciprocating compressors are driven by an external power source, usually an electric motor or an internal combustion engine. The motor or engine provides the energy needed to drive the piston.
- Cooling System: To dissipate heat generated during the compression process, reciprocating compressors often incorporate a cooling system. This may involve air or water cooling to maintain optimal operating temperatures.
Applications:
Reciprocating compressors find application in various industries and processes where the compression of gases is essential. Here are some common applications:
- Natural Gas Compression: Reciprocating compressors are widely used in the oil and gas industry for compressing natural gas. They help transport gas through pipelines.
- Petrochemical and Chemical Processing: In petrochemical and chemical plants, reciprocating compressors are employed for compressing gases involved in various processes, such as ethylene production and hydrogenation reactions.
- Refining Industry: Reciprocating compressors play a vital role in oil refineries, where they are used for processes like hydrocracking, catalytic cracking, and fluid catalytic cracking (FCC).
- Industrial Refrigeration: Reciprocating compressors are used in industrial refrigeration systems, particularly in applications where high compression ratios are required, such as low-temperature cold storage and freezing applications.
- Air Compression for Pneumatic Tools: Reciprocating air compressors are commonly used in workshops and manufacturing settings to power pneumatic tools such as drills, impact wrenches, and paint sprayers.
- Power Plants: Reciprocating compressors are employed in power plants for various purposes, including gas turbine inlet air compression, fuel gas boosting, and other auxiliary services.
The versatility, reliability, and efficiency of reciprocating compressors make them suitable for a wide range of applications across different industries, contributing to the smooth operation of various processes and systems.