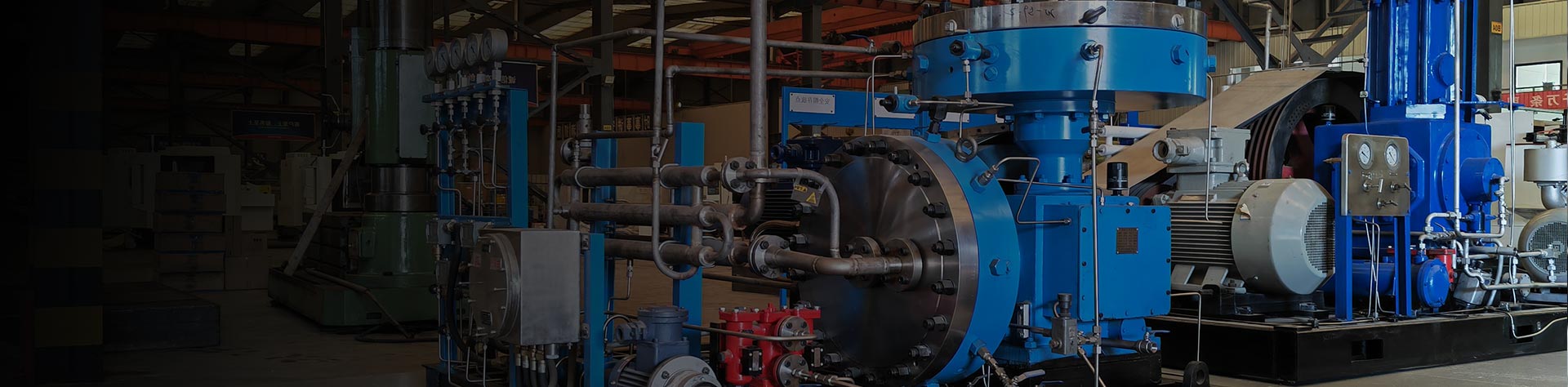
Diaphragm Compressor For On-Site Hydrogenation Station
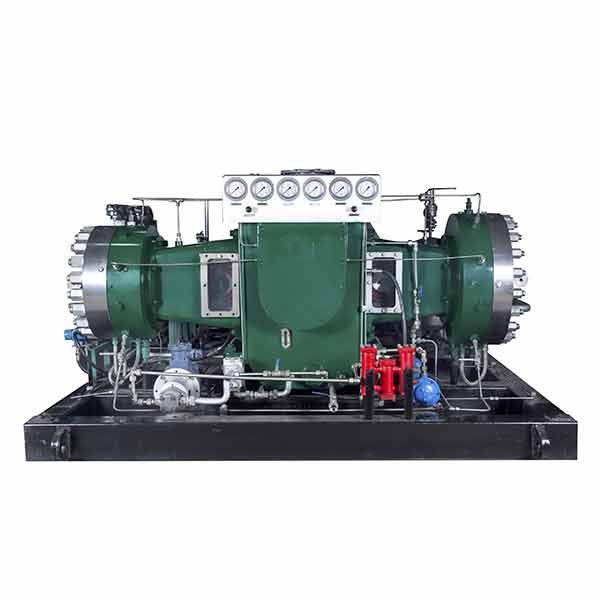
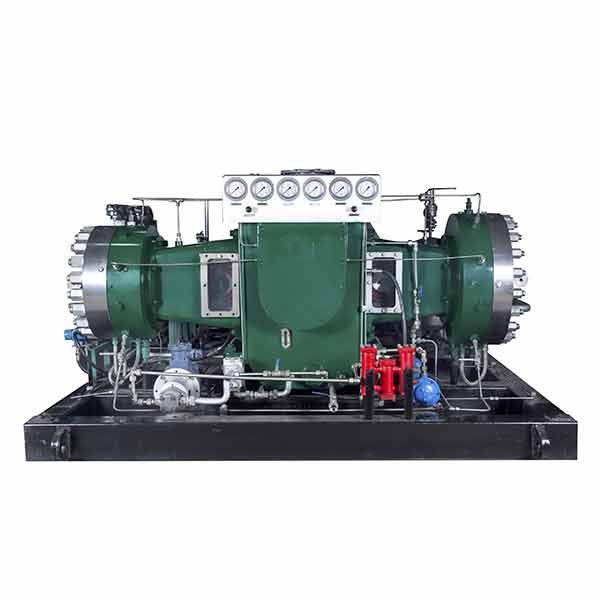
Diaphragm Compressor For On-Site Hydrogenation Station
- Max. discharge pressure 87MPa
- Flow Range 200~500NM3/h
- Motor Power 15~185kw
Description
A diaphragm compressor for on-site hydrogenation stations is a specialized piece of equipment designed for compressing hydrogen gas directly at the location where it is needed. Hydrogenation refers to the process of introducing hydrogen into a compound or material. In this context, on-site hydrogenation often involves supplying compressed hydrogen gas for various applications, such as fueling stations for hydrogen-powered vehicles, industrial processes, or other high-purity hydrogen applications.
Features & Characteristics:
Here are the key features of diaphragm compressor for on-site hydrogenation stations:
- Hermetic Sealing: The diaphragm compressor employs a flexible diaphragm or membrane as a crucial component. This diaphragm creates an airtight seal within the compression chamber. This feature is essential for maintaining the purity of the compressed hydrogen by preventing any external contamination.
- Safety Measures: Safety is paramount in hydrogen-related applications. Diaphragm compressors for on-site hydrogenation stations are equipped with advanced safety measures. This includes built-in leak detection systems that can quickly identify and respond to gas leaks.
- On-Site Compression: The on-site compression capability of this compressor is a significant advantage. Instead of relying on centralized compression facilities, on-site hydrogenation involves compressing hydrogen gas directly at the location where it will be used.
- Precision Engineering: Precision engineering is a hallmark of this diaphragm compressor. The controlled movement of the diaphragm ensures a tight seal and precise compression, contributing to the reliability and effectiveness of the compression process.
- Compliance with Standards: To ensure the highest safety and performance, the diaphragm compressor is designed and manufactured to comply with industry standards and regulations governing hydrogen compression and handling.
- Application Flexibility: The diaphragm compressor is adaptable to various settings and applications, making it suitable for integrating renewable energy sources.
Main Structure: Diaphragm compressor for on-site hydrogenation station
The main structure of a diaphragm compressor for on-site hydrogenation stations consists of several key components that work together to ensure efficient and reliable compression of hydrogen gas.
- Compression Chamber: The heart of the compressor, where hydrogen gas is compressed.
- Diaphragm: Flexible membrane separating gas and mechanical components, ensuring an airtight seal.
- Drive Mechanism: Powers the reciprocating motion of the diaphragm.
- Inlet and Outlet Valves: Control the hydrogen flow in and out of the compression chamber.
- Cooling System: Manages heat generated during compression, preventing overheating.
- Frame and Housing: Provides structural support, portability, and protection.
- Instrumentation and Sensors: Includes pressure and temperature sensors for real-time feedback.
Applications: Diaphragm compressor for on-site hydrogenation station
The Diaphragm compressor for the on-site hydrogenation station caters to a wide range of applications, including:
- Hydrogen-Powered Vehicles and Transportation: Beyond fueling stations, diaphragm compressors play a role in compressed hydrogen distribution for various forms of hydrogen-powered transportation, including delivery vehicles and trains.
- Hospitals and Laboratories: Applied in medical and research facilities for applications such as gas chromatography.
- Energy Storage Systems: Supports the compression of hydrogen for energy storage systems.
- Hydrogen Blending: Used in projects where hydrogen is blended with natural gas for industrial processes or injected into existing natural gas pipelines.