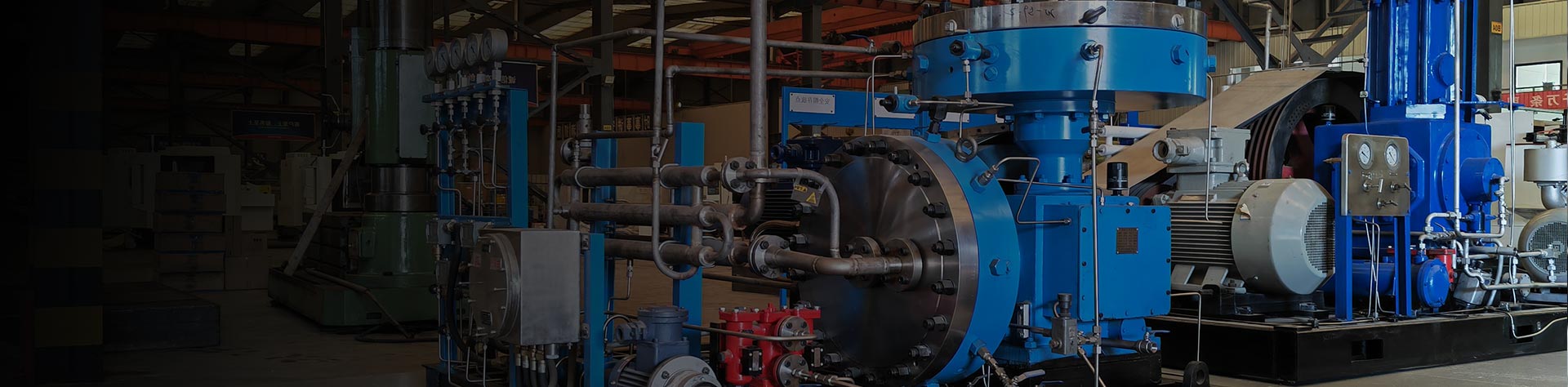
Chemical Process Compressors
Chemical Process Compressors
- Brand: Huayan Gas
- Place of Origin: China·Xuzhou
- Compressor structure: Piston Compressor
- Volume flow: 3NM3/hour~1000NM3/hour (customized)
- Voltage: 380V/50Hz (customized)
- Maximum outlet pressure: 100MPa (customized)
Get Free Quote
Description
Chemical Process Compressors refers to the reciprocating piston compressor used to compress various single or mixed medium gases in petroleum, chemical and other processes, and the chemical tail gas recovery and utilization system. Its main function is to transport the medium gas in the reaction device and provide the required pressure to the reaction device.
Features & Characteristics:
- Start-Up and Shutdown Systems: Efficient start-up and shutdown procedures are essential for chemical compressors. Systems may be in place to manage these transitions smoothly, minimizing stress on the equipment and ensuring a controlled process.
- Life Cycle Cost Analysis: When selecting chemical process compressors, consideration is given to the life cycle cost, which includes not only the initial purchase cost but also maintenance, energy consumption, and potential downtime costs over the expected lifespan of the equipment.
- Training and Documentation: Proper training materials and documentation are provided to operators and maintenance personnel to ensure the equipment is operated safely and effectively. This may include manuals, training programs, and access to technical support.
- Corrosion Protection: Given the corrosive nature of many chemical processes, compressors may have specialized coatings or corrosion-resistant materials to protect against the degradation of components over time.
- Redundancy and Reliability Enhancements: Critical chemical processes may require redundant compressor systems to ensure continuous operation in the event of a failure. Reliability enhancements such as predictive maintenance technologies may also be incorporated to detect potential issues before they lead to a breakdown.
Main structure: Chemical Process Compressors
- Compressor Housing: Outer casing for internal component protection.
- Rotor and Stator: Rotating and stationary elements facilitating compression.
- Cylinder: Compression chamber for gas compression, often in multiple stages.
- Valves: Inlet and discharge valves for gas flow control.
- Shaft Seal: Prevents gas leakage between rotating and stationary parts.
- Bearings: Reduce friction and support rotating elements.
- Lubrication System: Ensures proper lubrication for reduced wear.
- Cooling System: Manages heat through air or liquid cooling.
- Drive System: Powers the compressor (electric motor, gas turbine, etc.)
- The types of compressors are Z type, D type, and M type.
- The middle body of the slideway and the cylinder can be designed in different structural forms according to the process requirements.
Applications: Chemical Process Compressors
- Air Separation Plants: Chemical process compressors are used in air separation plants where atmospheric air is compressed and then separated into its constituent gases, such as nitrogen, oxygen, and argon, through cryogenic distillation.
- Polymer Production: In the production of polymers and plastics, chemical process compressors are involved in compressing and handling gases used in polymerization reactions, ensuring the proper conditions for forming polymer chains.
- Hydrogen Production: Chemical compressors are crucial in various hydrogen production methods, including steam methane reforming (SMR) and electrolysis. Hydrogen is compressed for storage and transportation in these processes.
- Pharmaceutical Industry: In the pharmaceutical industry, chemical process compressors are used to compress and handle gases involved in drug manufacturing processes, including synthesis and purification steps.
- Environmental Control Systems: Chemical compressors may be used in environmental control systems, such as those involved in capturing and compressing greenhouse gases for carbon capture and storage (CCS) initiatives.