Natural Compressor: A Guide to Understanding and Utilizing This Powerful Tool
Natural compressors are essential components of gas transportation and distribution infrastructure, helping increase pressure to mitigate frictional losses over long distance transit and decrease market volume distribution. They may also be utilized as waste gas recycling systems powering gas production plants or domestic households.
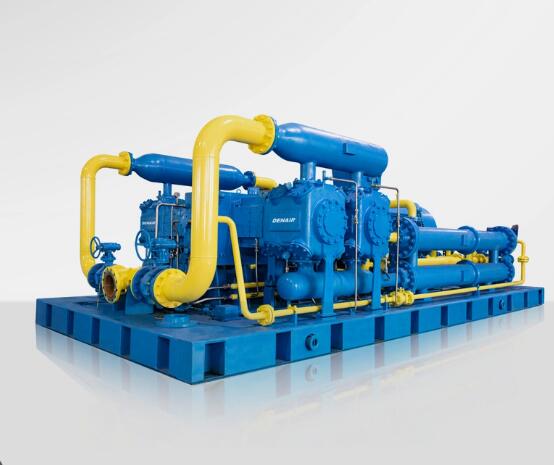
Fundamentally, natural gas compressors are designed to compress natural gas using various technologies such as positive displacement and dynamic compression, and then transport the compressed gas via pipelines to end-users. Furthermore, these machines may also be utilized in gas gathering, transmission and storage applications.
Key Takeaways
- Natural compressors are utilized to increase the pressure and volume of natural gas so it can be distributed more readily into the market.
- Natural compressors utilize various compression technologies, such as positive displacement and dynamic compression.
- Natural compressors can be utilized for various tasks, including gas collection, transmission, and storage.
Basic Compression Fundamentals: What You Should Know
Principles of Natural Compressors
Compressing natural gas requires increasing its pressure so it can flow more freely through pipelines, with natural gas compressors playing an essential role in this process. By compressing small volumes with forceful compression techniques and compressing at lower volumes, natural gas compression increases the pressure that then travels on its way toward its final destination.
Natural gas compressors are purposefully engineered to handle different varieties of natural gas, such as wet and dry gasses. Wet gas contains impurities like water or oil while dry gas does not; thus determining which type should be compressed ultimately comes down to what kind of natural gas you wish to compress.
Types of Natural Compressors
There are various types of natural gas compressors, including reciprocating compressors, centrifugal compressors, and rotary screw compressors. Reciprocating compressors are among the most commonly used natural gas compressors; they work by compressing gas by moving pistons back and forth within an enclosed cylinder to increase pressure by compressing more tightly.
Centrifugal compressors use a spinning impeller to compress the gas. By spinning rapidly at high speeds, centrifugal force generates centrifugal force which compresses it further – making these types of compressors suitable for high-volume, low pressure applications.
Rotary screw compressors use two interlocking rotating screws to compress gas, interlocking in opposite directions to reduce pressure while simultaneously compressing volume and increasing pressure – ideal for applications requiring both low volume and high-pressure applications.
Natural gas compression is an integral component of transporting natural gas through pipelines, with different kinds of compressors designed to compress different forms of natural gas. Therefore, an understanding of its principles and applications is vital when selecting an appropriate compressor for any particular task.
Applications of Natural Compressors
Natural compressors are versatile equipment used in various industries. Their primary function is increasing pressure in natural gas pipelines, warehouses or processing units to facilitate its transport more easily. Here are some uses of natural compressors:
Industrial Uses
Natural compressors find applications across several industries, including oil and gas, petrochemical, and manufacturing. Within oil and gas applications, natural compressors compress natural gas for transport through pipelines while simultaneously increasing production by raising well pressures; whereas in petrochemical firms they are used to compress hydrogen, nitrogen, and oxygen gasses used in various processes; manufacturing uses them to power pneumatic tools and equipment.
Environmental Impact
Natural compressors make an environmental difference. Their primary role is reducing greenhouse gas emissions by compressing natural gas – an emissions-free alternative fuel compared with fossil fuels – into compressed form for consumption by natural compressors. Furthermore, natural compressors are energy efficient – using less power for compressed natural gas than any other means would require.
Natural compressors play an indispensable role in many industries, helping increase natural gas pressure for easy transportation through pipelines, warehouses and processing units. Furthermore, these natural compressors have an environmental benefit by reducing greenhouse gas emissions while being energy efficient.
Design and Construction
Material Selection
Selecting appropriate materials for natural gas compressor stations is of utmost importance for safety and reliability in these facilities. Materials used should be durable enough to withstand both high pressure and corrosive natural gas conditions; noncombustible materials are preferred where there are gas pipes larger than 2 inches diameter present within buildings [1].
Pipes used for transporting gas must also be constructed of materials resistant to corrosion. Steel, plastic, and composite materials are among the materials often chosen as construction materials for pipelines; selection will ultimately depend on factors like gas pressure/temperature conditions as well as soil conditions at its location. [2].
Engineering Considerations
The design and construction of natural gas compressor stations must comply with all applicable federal regulations to ensure safety and reliability. The Federal Energy Regulatory Commission (FERC) is responsible for regulating the construction, operation, and maintenance of interstate natural gas pipelines and compressor stations [3].
The engineering considerations for natural gas compressor stations include the location of the station, the size and number of compressors, and the design of the piping system. The station must be located in an area where it can be easily accessed by fire-fighting equipment and emergency responders [1]. The size and number of compressors depend on the volume of gas that needs to be transported and the pressure required to move the gas through the pipeline.
Moreover, the piping system must be designed to minimize the risk of leaks, corrosion, and other potential hazards. The system must be able to withstand the high pressure and temperature of the gas and be resistant to corrosion. The design must also take into account factors such as the terrain, soil conditions, and environmental impact [2].
Overall, the design and construction of natural gas compressor stations require careful consideration of various factors to ensure safety and reliability. The selection of appropriate materials and compliance with federal regulations are crucial in ensuring the integrity of the facility.
[1] 49 CFR 192.163 — Compressor stations: Design and construction. (https://www.ecfr.gov/current/title-49/subtitle-B/chapter-I/subchapter-D/part-192/subpart-D/section-192.163)
[2] Understanding Natural Gas Compressor Stations – Penn State Extension (https://extension.psu.edu/understanding-natural-gas-compressor-stations)
[3] Natural Gas Compressor Stations – Interstate Natural Gas Association of America (https://ingaa.org/wp-content/uploads/2019/03/36048.pdf)
Operation of Natural Compressors
Natural compressors are used to increase the pressure of natural gas in pipelines, warehouses, or processing units. They are critical to the natural gas pipeline system, where they increase gas pressure and reduce its volume to make it distributable to the market.
Performance Metrics
The performance of natural compressors can be measured based on metrics such as flow rate, pressure ratio, and efficiency. Flow rate is the volume of gas that passes through the compressor per unit time. Pressure ratio is the ratio of the output pressure to the input pressure. Efficiency is the ratio of the actual work done by the compressor to the theoretical work required to compress the gas.
Natural compressors are designed to operate at a specific flow rate and pressure ratio. If the flow rate or pressure ratio exceeds the design limits, the compressor may become unstable and fail. Therefore, it is important to monitor the performance of natural compressors regularly and adjust the operating conditions when necessary.
Maintenance and Reliability
Natural compressors require regular maintenance to ensure their reliability and longevity. The maintenance activities include cleaning, inspection, lubrication, and replacement of worn-out parts. The frequency and scope of maintenance depend on the type of compressor, operating conditions, and manufacturer’s recommendations.
Regular maintenance can prevent unexpected downtime and reduce repair costs. It can also improve the efficiency and performance of the compressor. Therefore, it is important to establish a maintenance schedule and follow it rigorously.
In addition to maintenance, natural compressors require reliable and robust components to ensure their reliability. The components include valves, bearings, seals, and pistons. These components should be designed and manufactured to withstand the harsh operating conditions of natural gas compression.
Overall, natural compressors are critical to the natural gas industry, and their reliable operation is essential to the delivery of natural gas to consumers. By monitoring their performance, conducting regular maintenance, and using reliable components, natural compressors can operate efficiently and reliably for many years.
Technological Advancements

Innovations in Natural Compression
Natural gas compression has come a long way since its inception. The earliest forms of natural gas compression were done by hand, with workers using a hand crank to compress the gas. However, with the advent of new technologies, natural gas compression has become much more efficient and effective.
One of the most significant innovations in natural compression is the development of reciprocating compressors. These compressors use a piston to compress the gas, which is then released into a storage tank. Reciprocating compressors are highly efficient and can compress large volumes of gas quickly and easily.
Another significant innovation in natural compression is the use of rotary screw compressors. These compressors use two interlocking screws to compress the gas, which is then released into a storage tank. Rotary screw compressors are highly efficient and can compress large volumes of gas quickly and easily.
Future Trends
The future of natural gas compression is bright, with many new technologies on the horizon. One of the most promising technologies is the use of electric compressors. Electric compressors are highly efficient and can compress large volumes of gas quickly and easily. They are also much more environmentally friendly than traditional compressors, as they produce fewer emissions.
Another promising technology is the use of liquefied natural gas (LNG) compression. LNG compression is highly efficient and can compress large volumes of gas quickly and easily. It is also much more environmentally friendly than traditional compressors, as it produces fewer emissions.
Overall, the future of natural gas compression looks bright, with many new technologies on the horizon. As the demand for natural gas continues to grow, so too will the need for efficient and effective compression technologies.
Regulatory and Safety Standards

Compliance Requirements
Natural gas compressor stations are subject to various regulatory requirements to ensure compliance with environmental and safety standards. These requirements are set by federal agencies such as the Environmental Protection Agency (EPA) and the Occupational Safety and Health Administration (OSHA).
The EPA’s New Source Performance Standards (NSPS) for the oil and gas industry require compressor stations to reduce emissions of greenhouse gases, including methane. Compressor stations must also comply with the National Emission Standards for Hazardous Air Pollutants (NESHAP) for Natural Gas Transmission and Storage. Glycol dehydrators located at compressor stations are subject to these standards, with different requirements for large and small glycol dehydrators [1].
In addition to these federal regulations, compressor stations must comply with state and local regulations. For example, some states may require additional reporting or monitoring of emissions from compressor stations. Compressor station operators must also obtain permits from relevant agencies before construction and operation.
Safety Protocols
Compressor stations are subject to strict safety protocols to prevent accidents and ensure the safety of workers and nearby communities. OSHA sets standards for the use and storage of compressed gases, including requirements for valve protection for compressed gas cylinders and the use of safety devices to automatically cut off the flow of compressed air [2].
Compressor station operators must also follow safety protocols for the handling and transportation of natural gas. This includes regular inspections of equipment, emergency response plans, and training for workers on safety procedures.
Overall, compliance with regulatory and safety standards is essential for the safe and responsible operation of natural gas compressor stations. By following these requirements, compressor station operators can ensure the protection of the environment, workers, and nearby communities.
Market Analysis

The global natural compressor market is expected to grow significantly in the coming years. The market size is estimated at USD 42.04 billion in 2023 and is expected to reach USD 52.31 billion by 2028, registering a CAGR of 4.47% during the forecast period (2023-2028) 1.
Demand and Supply Dynamics
The demand for natural compressors is driven by the increasing demand for natural gas as an energy source and the growing liquefied natural gas (LNG) industry 2. The need for natural gas compressors is also driven by the increasing exploration and production activities in the oil and gas industry. The supply of natural compressors is expected to increase in the coming years as key players in the market are investing in R&D activities to develop advanced and efficient compressors.
Competitive Landscape
The natural compressor market is highly competitive with the presence of several key players such as Atlas Copco, Siemens, Ingersoll Rand, and General Electric 3. These players are focusing on expanding their product portfolio, investing in R&D activities, and entering into partnerships and collaborations to gain a competitive edge in the market. The market is also witnessing the entry of several new players, which is further intensifying the competition in the market.
In conclusion, the natural compressor market is expected to witness significant growth in the coming years driven by the increasing demand for natural gas and the growing LNG industry. The market is highly competitive with the presence of several key players who are investing in R&D activities to develop advanced and efficient compressors.
Footnotes
- Compressor Market Analysis, Size, Share – Industry Report ↩
- Natural Gas Compressor Market Report – Dataintelo ↩
- Compressor Market Size, Trends and Forecast to 2030 ↩
Challenges and Solutions

Technical Challenges
The natural gas industry faces a variety of technical challenges when it comes to compressor technology. One of the biggest challenges is accommodating the great variety in gas composition, including non-hydrocarbons such as hydrogen sulfide, carbon dioxide, and water vapor. Shale gas often contains particulates and contaminants that can shorten component life.
In addition, gas fields are rarely located close to where the energy is needed, so the gas needs to be transported by pipeline or ship. Pipelines are typically thousands of miles long, which presents challenges in terms of maintaining consistent pressure throughout the pipeline.
Another challenge is the need for subsea gas compression solutions. Several key components are well known from surface applications but need to be designed differently to meet the special subsea requirements.
Strategies for Optimization
There are several strategies for optimizing compressor technology in the natural gas industry. One solution for reliability is in the component design and in proper maintenance. This includes regular inspections and maintenance of the compressor components to ensure they are functioning optimally.
Another strategy is to use advanced controls and monitoring systems to optimize compressor performance. These systems can help identify potential issues before they become major problems, allowing for proactive maintenance and repairs.
Finally, in the face of global challenges to reduce greenhouse gas emissions and conserve natural resources, compressor technology will continually evolve to operate with greater efficiency and lower energy consumption. Since compressors are often driven by fossil fuels, this can have a significant impact on reducing the industry’s carbon footprint.
Overall, while there are certainly challenges to compressor technology in the natural gas industry, there are also many solutions available to optimize performance and ensure reliability. By leveraging advanced controls and monitoring systems, and by continuing to innovate in terms of component design and energy efficiency, the industry can continue to meet the growing demand for natural gas while minimizing its impact on the environment.
Frequently Asked Questions

How do natural gas compressors work in residential settings?
Natural gas compressors used in residential settings work by compressing natural gas to increase its pressure so that it can be transported through pipelines. The compressor takes in gas from the pipeline and compresses it to a higher pressure, which allows it to travel further through the pipeline. The compressed gas is then sent to the next compressor station, where the process is repeated.
What are the leading manufacturers of natural gas compressors?
There are many manufacturers of natural gas compressors, including Ariel Corporation, GE Oil & Gas, Siemens, and Dresser-Rand. These companies produce compressors that are used in a variety of applications, including natural gas pipelines, gas processing plants, and storage facilities.
What are the differences between small and large natural gas compressors?
Small natural gas compressors are typically used in residential settings and have a lower capacity than larger compressors. They are also usually powered by electricity. Large natural gas compressors, on the other hand, are used in industrial settings and have a higher capacity. They can be powered by a variety of sources, including natural gas, diesel, and electricity.
How does an electric natural gas compressor differ from other types?
An electric natural gas compressor is powered by electricity and is typically used in smaller applications, such as residential settings. They are generally more efficient than other types of compressors and produce less noise. Other types of compressors, such as reciprocating and rotary screw compressors, are typically used in larger applications and can be powered by a variety of sources.
What are the common types of compressors used at natural gas compressor stations?
The most common types of compressors used at natural gas compressor stations are reciprocating compressors and centrifugal compressors. Reciprocating compressors use pistons to compress the gas, while centrifugal compressors use a spinning impeller to increase the gas pressure. Both types of compressors are used in a variety of applications, including natural gas pipelines, gas processing plants, and storage facilities.
How is natural gas compressed and stored safely?
Natural gas is compressed using a variety of techniques, including reciprocating compressors, centrifugal compressors, and rotary screw compressors. Once the gas is compressed, it is stored in tanks or pipelines until it is ready to be transported. Safety measures are in place to ensure that the gas is stored and transported safely, including pressure relief valves, automatic shutdown systems, and emergency response plans.