Membrane Compressor: Working Principle, Applications
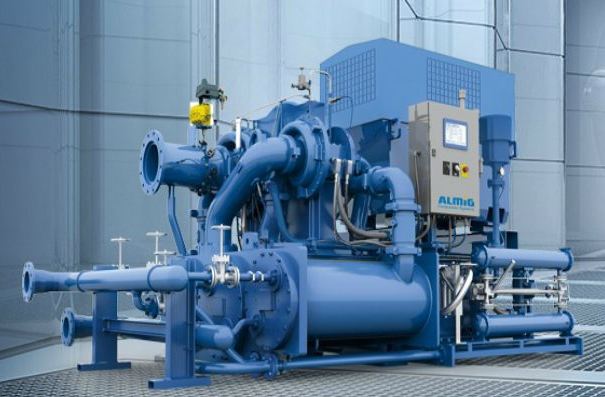
Introduction
Membrane compressor play a pivotal role in various industries, offering efficient and sustainable solutions for gas compression and separation. In this comprehensive guide, we will delve into the working principle, applications, and advantages of membrane compressors. Whether you are an industry professional seeking to understand this technology better or a curious mind looking to explore innovative solutions, this guide has you covered.
Definition of Membrane Compressor
A membrane compressor, also known as a gas compressor, is a mechanical device designed to increase the pressure of a gas by reducing its volume. Unlike traditional compressors that use pistons or rotary mechanisms, membrane compressors rely on flexible membranes to achieve compression.
Significance in Various Industries
The significance of membrane compressors cannot be overstated, as they find applications in diverse industries, including petrochemical, food and beverage, medical, and more. These compressors are instrumental in processes such as gas separation, packaging, and medical gas supply, contributing to improved efficiency and sustainability.
Purpose of the Guide
The purpose of this guide is to provide a comprehensive understanding of membrane compressors, from their working principles to real-world applications. By the end of this guide, you will gain insights into how these compressors operate, where they are used, their advantages, and the future trends in this evolving technology.
Membrane Compressor Working Principle
How Membrane Compressors Operate
At the heart of a membrane compressor is a flexible membrane or diaphragm that separates the compression chamber into two sections: the high-pressure and low-pressure sides. When the compressor is in operation, the membrane flexes back and forth, creating changes in volume that result in gas compression.
Key Components and Materials
Membrane compressors consist of several key components, including the membrane, support structure, inlet and outlet valves, and a drive mechanism. Membranes are typically made from high-strength materials like elastomers or polymeric films, ensuring durability and reliability in various operating conditions.
Compression Process Explained
The compression process in a membrane compressor involves the cyclic movement of the membrane. As the membrane moves outward, the volume of the low-pressure side increases, causing gas to be drawn in. When the membrane moves inward, the volume decreases, compressing the gas and increasing its pressure. This continuous back-and-forth motion results in the desired compression.
Applications of Membrane Compressors
Industrial Uses in Gas Separation
Membrane compressors are widely employed in industrial gas separation processes. They are used to separate gases based on their molecular size and permeability through the membrane. This technology is crucial in producing high-purity gases for industrial applications, including nitrogen generation and hydrogen purification.
Food and Beverage Industry Applications
In the food and beverage industry, membrane compressors play a crucial role in packaging and preserving products. They are used for filling gas into food packaging to extend shelf life, preventing spoilage and ensuring product freshness. Additionally, membrane compressors are employed in carbonation processes for beverages.
Medical and Healthcare Utilization
The medical and healthcare sector heavily relies on membrane compressors for the supply of medical gases such as oxygen and nitrous oxide. These compressors ensure a consistent and reliable source of gases that are essential for various medical procedures, from anesthesia to respiratory therapy.
Advantages of Membrane Compressors
Energy Efficiency
One of the significant advantages of membrane compressors is their energy efficiency. Unlike traditional compressors, which may have high energy consumption, membrane compressors operate with minimal energy input. This efficiency translates to cost savings and reduced environmental impact.
Environmental Benefits
Membrane compressors contribute to environmental sustainability. They produce fewer emissions, making them an eco-friendly choice for gas compression. Additionally, their energy-efficient operation reduces the carbon footprint, aligning with global efforts to combat climate change.
Maintenance and Reliability
Membrane compressors are known for their low maintenance requirements and high reliability. With fewer moving parts compared to traditional compressors, they experience less wear and tear, resulting in longer service life and reduced downtime.
Membrane Compressor Types
There are several types of membrane compressors, each tailored to specific applications and operational requirements. Understanding these types is essential for selecting the right compressor for a given task.
Diaphragm-Type Membrane Compressors
Diaphragm-type membrane compressors use a flexible diaphragm to separate the compression chamber. They are suitable for applications that require high compression ratios and can handle a wide range of gas compositions.
Bellows-Type Membrane Compressors
Bellows-type membrane compressors employ a bellows-like structure to achieve compression. They are commonly used in applications where precision and control are critical, such as laboratory settings.
Fiber-Type Membrane Compressors
Fiber-type membrane compressors utilize a membrane made of fine fibers. These compressors are ideal for processes that involve corrosive gases or where high purity is essential, such as semiconductor manufacturing.
Membrane Compressor Selection Criteria
Choosing the right membrane compressor involves considering several factors to meet specific operational needs and industry requirements.
Capacity and Flow Rate Requirements
Determining the required capacity and flow rate is crucial. Different applications demand varying levels of compression, and selecting a compressor that can meet these requirements is essential.
Gas Composition Considerations
The composition of the gas being compressed is a critical factor. Some gases may be corrosive or reactive, necessitating the selection of materials that can withstand such conditions.
Specific Industry Needs
Each industry has unique needs and regulations. It is essential to consider industry-specific requirements when selecting a membrane compressor to ensure compliance and optimal performance.
Membrane Compressor Manufacturers and Models
Leading Manufacturers in the Industry
Several reputable manufacturers specialize in membrane compressors, offering a range of models to cater to diverse applications. Some prominent manufacturers include [Manufacturer A], [Manufacturer B], and [Manufacturer C].
Highlighted Models and Their Features
Let’s take a closer look at a few highlighted models from leading manufacturers and their standout features:
- Model X from Manufacturer A
- High compression ratio for gas separation applications.
- Robust construction for durability in industrial settings.
- Energy-efficient design to reduce operational costs.
- Model Y from Manufacturer B
- Precise control and low pulsation for laboratory use.
- Compatibility with a wide range of gases, including corrosive ones.
- Compact and space-saving design.
- Model Z from Manufacturer C
- Exceptional purity and high flow rates for semiconductor manufacturing.
- Advanced materials resistant to aggressive gases.
- Smart control system for remote monitoring and optimization.
Case Studies
Real-World Applications of Membrane Compressors
To illustrate the practicality and effectiveness of membrane compressors, let’s explore some real-world applications:
Case Study 1: Nitrogen Generation in Electronics Manufacturing
In the electronics manufacturing industry, nitrogen is used for various purposes, including soldering and preventing oxidation. Membrane compressors are employed to generate high-purity nitrogen on-site, reducing the need for nitrogen cylinders and transportation costs.
Case Study 2: Medical Gas Supply
Hospitals and healthcare facilities rely on a consistent supply of medical gases, such as oxygen and nitrous oxide. Membrane compressors ensure a reliable source of these gases, supporting critical medical procedures and patient care.
Success Stories and Performance Improvements
Success stories abound in industries that have adopted membrane compressor technology. Improved efficiency, reduced operating costs, and enhanced product quality are common outcomes. These compressors continue to evolve, offering even greater performance and versatility.
Future Trends in Membrane Compressor Technology
As technology continues to advance, membrane compressors are poised for further innovation and growth. Here are some future trends to watch:
Advancements in Membrane Materials
Research into novel membrane materials will lead to improved gas separation capabilities and increased resistance to harsh conditions. These materials will expand the range of gases that membrane compressors can handle.
Digitalization and Smart Control Systems
Integration of digitalization and smart control systems will enhance the monitoring and optimization of membrane compressors. Remote diagnostics and predictive maintenance will become standard features, reducing downtime and maintenance costs.
Sustainability Initiatives
Membrane compressors will play a crucial role in sustainability initiatives. Their energy-efficient operation and reduced emissions align with the global push for greener technologies. Membrane compressor manufacturers will continue to focus on eco-friendly solutions.
Conclusion
In conclusion, membrane compressors are versatile and efficient devices that have revolutionized gas compression and separation across various industries. Their energy efficiency, environmental benefits, and reliability make them indispensable in today’s ever-evolving industrial landscape. As technology continues to advance, we can look forward to even more innovative applications and improved performance from membrane compressors. Whether you are in the petrochemical, food, medical, or any other industry, exploring membrane compressor technology is a step toward a more sustainable and efficient future. Embrace this innovative solution and unlock its potential in your operations. The journey of discovery in membrane compressor technology is just beginning, and the possibilities are boundless.