Revolutionizing Compression: The Science and Applications of Membrane Compressors
For numerous industrial purposes, conventional compression techniques have been employed to elevate the pressure of gases and liquids. These conventional approaches predominantly utilize mechanical systems, including piston and screw compressors. Nonetheless, the growing demand for compression solutions that are both more efficient and eco-friendly has given rise to the membrane compressor. These pioneering devices utilize flexible membranes to achieve compression, providing benefits such as oil-free operation, decreased maintenance requirements, and improved sustainability.
The Science Behind Membrane Compressors
Membrane compressors operate on the fundamental principle of using a flexible membrane to displace and compress gases. This process relies on the elasticity of the membrane material, which deforms when subjected to pressure differentials. Here’s a brief insight into the science behind membrane compressors:
Basic Principles of Membrane Compression
Membrane compressors consist of a chamber with a flexible membrane separating two sections. As gas is introduced into one side of the chamber, the membrane flexes and expands, compressing the gas on the other side. The cyclic motion of the membrane, driven by external mechanisms, facilitates the compression and expulsion of the gas.
Material Selection and Design Considerations
Membrane materials must exhibit high elasticity, durability, and resistance to fatigue. Common choices include 00Cr15Ni5. Design considerations include membrane thickness, shape, and size, as these factors impact compression efficiency and lifespan.
Advantages Over Traditional Compression Methods
Membrane compressors offer several advantages compared to traditional mechanical compression methods like piston or screw compressors. These include:
- Oil-Free Operation: Membrane compressors are inherently lubricant-free, eliminating the risk of oil contamination in compressed gases.
- Reduced Maintenance: The absence of complex moving parts results in lower maintenance requirements and longer service life.
- Enhanced Sustainability: Membrane compressors are energy-efficient and environmentally friendly, contributing to sustainability goals.
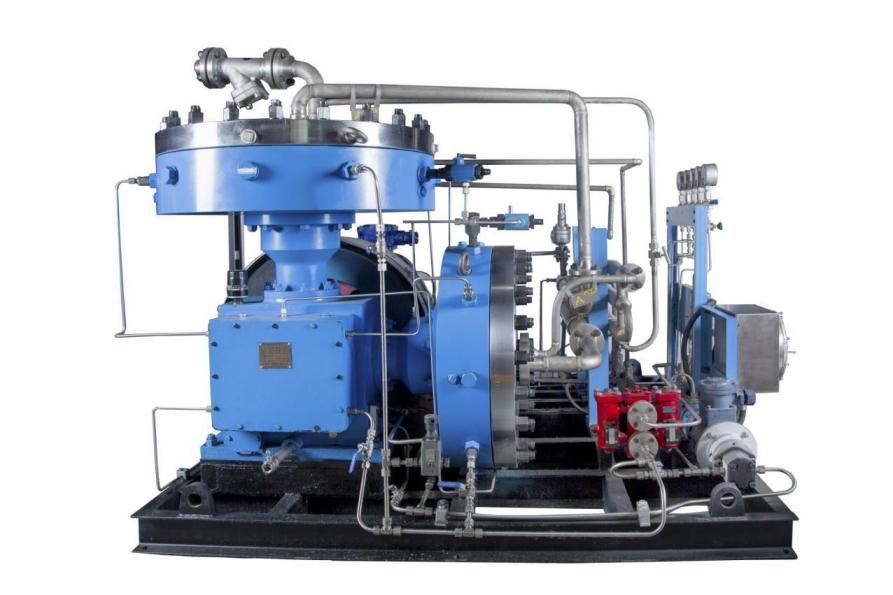
Key Components and Their Roles in Membrane Compressors:
Membrane Materials
- Pros: Membrane materials, typically elastomers like 00Cr15Ni5, provide the essential flexibility required for compression. They deform under pressure differentials, facilitating gas compression. Their elasticity and resilience are advantageous for repeated cycles.
- Cons: Membrane materials must be carefully chosen to suit the specific application, as they can be sensitive to temperature extremes, chemical exposure, and wear over time. Material selection is critical to ensure long-term durability and performance.
Supporting Infrastructure and Equipment
- Pressure Chamber: This chamber houses the gas to be compressed and the membrane. It plays a central role in creating the pressure differential that drives compression.
- Drive Mechanism: External mechanical systems, such as motors and pistons, provide the force necessary to deform the membrane and initiate compression cycles.
- Valves and Controls: These components regulate gas flow in and out of the compression chamber, ensuring efficient compression and system stability.
- Cooling Systems: In some cases, cooling systems may be necessary to manage temperature increases during compression.
Applications in Various Industries
Membrane compressors find diverse applications across various industries, offering innovative solutions and advantages:
Oil and Gas
Membrane compressors improve the efficiency of gas extraction and transportation processes. They help compress natural gas for pipeline transmission and enhance recovery methods, making operations more cost-effective and environmentally friendly.
National Defense
Membrane compressors are employed in military applications to provide high-pressure gases for weapons systems, missile launchers, and submarine propulsion, ensuring national security.
Chemical Industry
In the chemical sector, membrane compressors facilitate the compression of various gases, enhancing safety and efficiency in processes like gas separation, chemical synthesis, and storage, contributing to the industry’s productivity and product quality.
Other Industries
Membrane compressors also find applications in aerospace for cabin pressurization, in environmental monitoring for air sampling, and in laboratories for analytical instruments. Their reliability and oil-free operation make them valuable across a wide range of industrial settings.
Advantages of Membrane Compressors
Enhanced Energy Efficiency
Membrane compressors inherently excel in energy efficiency by eliminating the mechanical friction and oil lubrication necessary for conventional compressors. This results in decreased energy consumption and operational expenses.
Environmental Friendliness
Through their oil-free operation, membrane compressors effectively mitigate the risk of oil contamination in compressed gases, positioning them as environmentally sound options. They contribute to sustainability objectives by curbing carbon emissions.
Versatile Scalability and Adaptability
The compact design and minimal maintenance requirements of membrane compressors render them highly adaptable to diverse settings. They can be easily adjusted in size to accommodate the specific demands of various applications.
Challenges and Constraints
Critical Material Selection
Optimal membrane material selection is paramount, as it must withstand operational conditions and chemical exposure. Inappropriate material choices can result in degradation and diminished performance.
Pressure Constraints
Membrane compressors may have limitations when it comes to achieving extremely high pressures, which can curtail their suitability for select industrial uses, especially those requiring exceptional pressure levels.
Initial Investment
While membrane compressors may entail a higher initial cost compared to traditional compressors, it’s worth noting that the long-term energy savings and reduced maintenance expenses often justify this upfront expenditure.
Case Studies
Case Study 1: Chemistry Indurstry
One of the primary benefits of our membrane compressor is its ability to achieve exceptionally high gas purity levels, ensuring superior quality and performance in chemistrial applications.
Case Study 2: Food Packaging
A leading food packaging company adopted membrane compressors to extend product shelf life. The technology’s oil-free operation prevented food contamination, and the reduction in maintenance costs led to significant savings. This case underscores the value of membrane compressors in enhancing food quality and cost-efficiency in the food and beverage industry.
Future Prospects and InnovationsMaterials Advancements
Ongoing developments in material science are likely to yield even more durable and efficient membrane materials, expanding the capabilities and lifespan of membrane compressors.
Growth Areas
Membrane compressors are poised for growth in sectors such as renewable energy, where hydrogen compression for fuel cells is crucial, and in water treatment for efficient aeration. Their role in sustainability and green technologies is expected to expand.
Integration with IoT and AI
Integration with IoT and AI technologies will enable predictive maintenance, real-time monitoring, and optimization of membrane compressors, enhancing their reliability and efficiency in various applications.
CONCLUSION
In the realm of compression technology, membrane compressors represent a remarkable evolution. Their blend of energy efficiency, environmental friendliness, and adaptability makes them potent contenders for a wide range of industrial applications. As materials science continues to advance and technology integration deepens, membrane compressors are poised to lead the way in revolutionizing how we compress gases and fluids, driving us toward a more sustainable and efficient future across diverse industries.