Increase Oil & Gas Production: Powerful Oilfield Compressor
The Powerhouse of Production: A Comprehensive Guide to Oilfield Compressors
Modern civilization depends on oil and gas, which must be extracted, processed, and transported via a sophisticated network of machinery. Among these indispensable instruments is the oilfield compressor, a beast that powers numerous vital operations in the upstream segment of the oil and gas business. This piece explores the world of oilfield compressors, looking at different kinds, uses, advantages, and important factors to take into account when choosing the best one for your requirements.
Unveiling the Workhorses: Types of Oilfield Compressors
Different versions of oilfield compressor are available, each designed to handle a particular task in the oil and gas production cycle. The three most prevalent kinds are broken out as follows:
- Reciprocating Compressors:
In oilfields, reciprocating compressors are the most commonly utilized form of workhorse. To compress gas, they use pistons that move back and forth inside a cylinder. High-pressure capabilities make reciprocating compressors ideal for a wide range of uses, such as gas lift, wellhead compression, and reinjection.
- Centrifugal Compressors:
Designed for high-volume gas transportation in pipelines, centrifugal compressors use a revolving impeller to boost gas velocity. When compared to reciprocating compressors, they have a higher-pressure output yet operate more smoothly and efficiently overall.
- Screw Compressors:
Increasingly in demand because of its small size and effective operation, screw compressors compress gas using intermeshing screws. They are ideal for a variety of applications, including gas lift and reinjection, because they offer a good balance between pressure and flow rate.
The Power of Compression: Applications of Oilfield Compressors
The heroes of the oil and gas sector are oilfield compressor. This strong equipment is essential to the extraction, processing, and transportation of these precious commodities at different phases of the production process. Now let us examine the crucial uses for which oilfield compressors are highly effective:
- Boosting Production with Gas Lift
Gas lift can be used to increase production in an established oilfield where the natural reservoir pressure is declining. Oilfield compressors are helpful in this situation. To maximize the potential of the well, they inject compressed gas down the wellbore, lightening the fluid column and allowing for enhanced oil output.
- Managing Pressure Drops in the Wellhead
Pressure naturally drops when gas and oil move from the reservoir to the surface. Here, wellhead compressors are the main attraction. They effectively increase pressure, facilitating the efficient and seamless flow of gas and oil via pipelines to processing facilities.
- Rejuvenating Reservoirs by Downhole Injection
For the best oil and gas recovery, reservoir pressure must be maintained. An essential component of enhanced oil recovery (EOR) methods is oilfield compressors. They replenish the reservoir with natural gas, preserving pressure and releasing more resources.
- Processing of Natural Gas: Separation Powerhouse
Natural gas travels further when it is extracted. Valuable natural gas liquids (NGLs) must be extracted from the raw gas stream during processing. Oilfield compressors, which apply different degrees of compression during the separation stages, are crucial components of this process.
- High-Pressure Gas Transfer: Powering Extended Distance Travel
Sufficient pipeline pressure must be maintained to deliver natural gas to remote consumers. The problem is taken up by oilfield compressors, which guarantee effective long-distance transmission through these essential energy sector arteries.
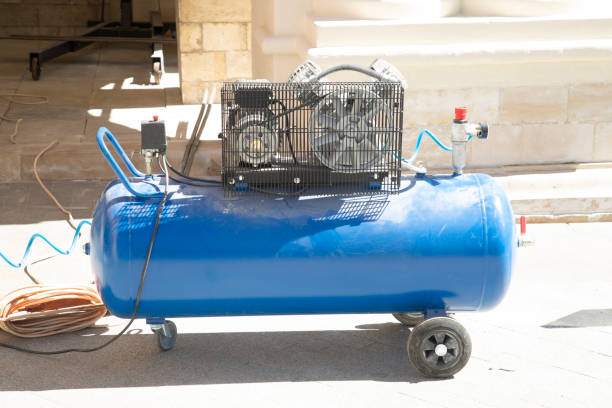
Beyond Efficiency: Unveiling the Multifaceted Benefits of Oilfield Compressors
They are more than just strong air-squeezing devices. They are priceless resources in the oil and gas sector because they provide a plethora of advantages that go well beyond simple efficiency. Let’s examine these benefits that will help energy exploration become more fruitful and sustainable in the future:
- Output Powerhouse:
Their capacity to have a direct influence on output is their main advantage. Oilfield compressor contribute significantly to an increase in oil and gas recovery by enabling effective transportation through wellhead compression and by maintaining reservoir pressure through gas lift and injection.
- Cost-Conscious Operations:
Efficiency is the priority for modern compressors. Cutting-edge designs maximize energy use, which saves operational expenses for producers of natural gas and oil. This results in more profitability and a stronger competitive advantage in the international market.
- Maximum Adaptability:
The wide variety of screw, centrifugal, and reciprocating compressor types provides unparalleled operational flexibility. Producers may guarantee excellent performance and efficiency across a range of jobs by choosing the compressor that best suits their needs.
Resilience is a key component of oilfield compressor engineering. They are built to survive high temperatures, challenging conditions, and constant use. This translates to consistent performance, less downtime, and seamless manufacturing procedures.
- Environmental Responsibilities:
Although the oil and gas sector has environmental issues, oilfield compressors can help to mitigate such issues. Through process optimization and energy waste minimization, they help to lessen their environmental impact. Some compressors also use fuels that burn cleaner, which lowers emissions even further.
- The Path to Success:
These compressors offer advantages beyond just instantaneous output. They open the door for the oil and gas sector to have a more sustainable future. Oilfield compressors provide cost-effectiveness, efficiency, and environmental responsibility, enabling producers to run their businesses profitably and responsibly.
Choosing the Right Oilfield Compressor: Tailoring Power to Your Needs
There is no one-size-fits-all method when it comes to choosing the best compressor. These strong machines are available in many configurations, each of which is best suited for a particular task. Several important elements need to be carefully considered to guarantee optimal performance and prevent expensive mismatches. Let’s investigate this method of making decisions:
- Recognizing the Task at Hand:
The first step is determining the compressor’s intended purpose. Will it be in charge of pipeline gas transportation, downhole gas injection, wellhead pressure booster, and gas lift? Determining the main use facilitates the selection of appropriate compressor types.
- Fuelling Your Requirements: The King is Capacity
Once you are aware of the task, identify the necessary “muscle.” This corresponds to pressure output and flow rate, or the amount of gas handled per unit of time. A thorough analysis of your unique production requirements guarantees that the selected compressor has enough power to complete the task effectively.
- Environmental Factors to Be Considered Be Prepared:
Don’t undervalue the influence of the work environment. Altitude, temperature, and humidity can all affect how well a compressor works. Selecting a model made specifically for your environment ensures peak performance and guards against overheating or other performance problems.
- Expense-effectiveness: Efficiency Counts
Operating costs are directly correlated with energy use. It is essential to assess the energy efficiency of various compressor types. With their cutting-edge features, modern compressors use less energy and save money over time.
- Matters of Maintenance: Organizing Maintenance
A machine can never run indefinitely. Give priority to compressors with well-established service support networks and easily accessible spare parts. Reducing maintenance downtime enhances profits and guarantees smooth operation.
Keeping Your Workhorse Running Smoothly: Oilfield Compressor Maintenance Tips
Compressors used in oilfields are essential to the effective production of gas and oil. Like any hardworking machine, they require regular maintenance to operate at their best, have the least amount of downtime, and last longer. To ensure the proper operation of your oilfield compressor, follow these important maintenance guidelines:
- Regular Oil Changes and Filter Replacements:
Oil functions as the lifeblood of your compressor, lubricating moving parts and avoiding wear and tear. When changing your compressor’s oil, heed the manufacturer’s recommendations and use the right kind and grade of oil. Remember to use air filters! Airflow is restricted by clogged filters, which lowers efficiency. Plan for routine replacements to guarantee top performance.
- Inspection is Vital: Preventive care is essential
To spot possible issues before they become serious, do routine inspections. Check for belt and hose wear indicators, leaks, and loose connections. Promptly resolving these problems guarantees safe functioning and avoids expensive malfunctions.
- Cooling System Maintenance:
When oilfield compressors are operating, they produce a lot of heat. For the temperature to remain at its ideal level, the cooling system is essential. To guarantee effective heat dissipation, clean heat exchangers and radiators regularly. Check coolant levels and keep an eye on its condition by adhering to the manufacturer’s recommendations.
- Training and Expertise:
While routine maintenance procedures are crucial, certain jobs call for specialist knowledge. By providing your staff with instruction on fundamental compressor maintenance procedures, you may enable them to recognize and resolve small problems. Nonetheless, seeking advice from a trained oilfield compressor service provider is always advised for intricate repairs or troubleshooting.
You can make sure this compressor keeps performing at its best for many years by putting these maintenance suggestions into practice and creating a proactive maintenance routine. Recall that a well-maintained compressor maximizes return on investment, increases productivity, and decreases downtime.
Conclusion:
To save operating expenses and provide a comfortable working environment, we place a high priority on efficiency and quiet operation. For experienced operators or those starting a new project, LEIYAO compressor enables you to maximize output while putting environmental stewardship first. Explore the LEIYAO range on our website today to find the ideal compressor to advance your business.