How Do Gas Compressor Machines Work? Explained Simply
The Power of Gas Compressor Machine: Applications, Types, and Essential Know-How?
The humble gas compressor machine is an essential component of many different applications and industries. These devices are the workhorses behind compressed air, a useful and necessary resource that powers everything from our freezers to industrial activities. This thorough book explores the world of gas compressor machine, including their inner workings, many uses, and important things to keep in mind.
Understanding the Fundamentals: How Gas Compressors Work?
A gas compressor machine primary function is to raise a gas’s pressure. This is accomplished by several methods, the most popular ones using centrifugal impellers, rotors, and pistons. This is a condensed explanation of the procedure:
- Piston Compressors:
Working similarly to an automobile engine, a piston compressor draws in gas, compresses it, and releases it at a greater pressure using a reciprocating piston inside a cylinder.
- Rotary Screw Compressors:
Compressors with rotary screw technology use meshed rotors that spin inside a chamber to capture and compress the gas. They are ideal for continuous-duty applications and provide smooth operation.
- Centrifugal Compressors:
Using a high-speed impeller, centrifugal compressors give the gas kinetic energy that diffuses through the housing to become pressure. These compressors are excellent at managing big gas volumes.
The Diverse Applications of Gas Compressor Machines:
A surprisingly broad number of businesses use gas compressors. Here are a few well-known instances:
- Industrial Processes:
Compressors are essential for a variety of industrial processes, ranging from powering pneumatic equipment in manufacturing facilities to operating air separation units to produce industrial gases.
- Oil and Gas Industry:
Exploration, transportation, and processing of oil and gas depend heavily on gas compressors. They are used for long-distance pipeline gas transportation as well as for injecting natural gas back into subterranean reserves for improved recovery.
- Food and Beverage Industry:
The bottling, packing, and processing of food all depend heavily on compressed air. Pneumatic conveyance, mixing, and process control are all done with compressors.
- Air Conditioning Systems:
Gas compressors are used by air conditioners and refrigerators to move refrigerant, which is essential to the cooling process.
- Construction Industry:
Drilling, sandblasting, and demolition are just a few of the jobs that require pneumatic instruments that run on compressed air.
Safety First: Powering Through with Gas Compressor Precautions
Gas compressors are strong devices that supply a crucial compressed air supply to a variety of businesses. But because of their enormous potential, operating safety must also come first. The following are essential safety measures to provide a secure and efficient work environment:
- Owner’s Manual: Your Bible of Safety:
Think of the owner’s manual as your bible for safety. It includes comprehensive guidelines on safe operation practices that are particular to the compressor type you own. Before you turn on the machine, familiarize yourself with these instructions.
- Put on the Correct Gear:
Personal protective equipment (PPE) is the first step toward safety. To protect your eyes from flying debris and any fluid spills, always wear the proper safety glasses. To protect against high noise levels, ear protection may be required depending on the application. To safeguard your hands when performing operations requiring pressurized air discharge, think about using gloves.
- Remain Safe:
The force of compressed air is strong. When using the equipment, always keep a safe distance from the discharge outlet of the compressor. By doing this, one can prevent unintentional exposure to a high-pressure air explosion that could result in severe harm. Generally, the recommended safe operating distance for your particular compressor type will be specified in the manufacturer’s handbook.
- Keep it Clear:
There should be no obstacles in the way of the compressor’s surroundings. This permits safe access for maintenance and operation and permits adequate airflow, reducing overheating. Steer clear of operating the compressor in dangerous environments or storing combustible goods.
Watch Out for Condensation:
While operating, gas compressors may produce condensation. Water buildup in the compressed air system should be avoided since it can cause equipment damage or corrosion. Occasionally clearing condensation accumulation with a drain valve is advised per the manufacturer’s instructions.
You may make the operation of your gas compressor profitable and risk-free by following these safety guidelines. Recall that everyone dealing with compressed air systems must practice safety; it is not a recommendation.
Selecting the Perfect Gas Compressor: A Type Guide:
The workhorses of compressed air and gas compressors drive everything from your home refrigerator to industrial operations. But there are so many kinds to choose from that it might be intimidating. This article explores the three primary categories of gas compressors and assists you in selecting the ideal model for your requirements.
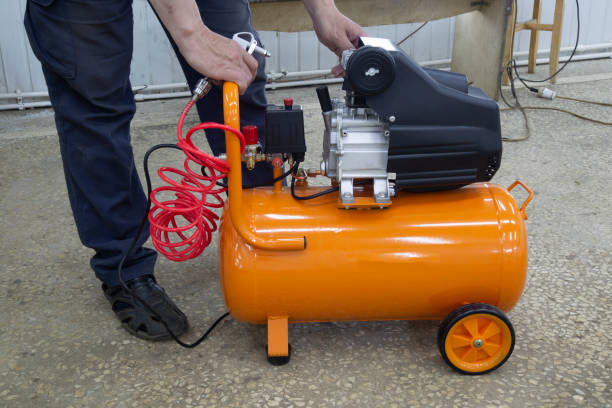
Piston Compressors:
These dependable devices compress air by use of pistons that travel within cylinders. Their exceptional pressure capabilities make them ideal for applications with variable pressure demands that need intermittent operation. Typically, they may be found in:
- Providing electricity to operate pneumatic instruments, such as impact wrenches and tire inflation machines.
- Construction sites are utilized for nail gun powering, demolition, and sandblasting. It is perfect for DIY tasks, paint sprayer operation and tire inflation. Visit China Compressors to see our extensive selection of piston compressors.
Rotary Screw Compressors:
Intermeshing rotors on these workhorses capture and compress air as they revolve. Their continuous duty capabilities, excellent efficiency, and seamless operation are well-known attributes. They are perfect for:
- Providing compressed air to run equipment, move materials, and run control systems.
- Used for running bottling machinery, mixing procedures, and pneumatic conveying.
- They supply several tools with continuous power from a dependable compressed air source.
Centrifugal Compressors:
By using impellers to accelerate air, these high-speed devices transform kinetic energy into pressure. They are quite good at managing big air volumes at moderate pressures. They are frequently employed in:
- For long-distance pipeline transportation of natural gas.
- It is Adding air to wastewater to help organic materials break down biologically.
- Capsules are propelled quickly via pressured tubes using pneumatic tube systems.
Choosing the Right Compressor:
The best choice of compressor is contingent upon many factors:
- Application:
Determine the air volume (CFM) and pressure needed for your particular application.
- Duty Cycle:
Take into account the frequency of usage of the compressor, either on a continuous or intermittent basis.
- Power Source:
Depending on your requirements and application, select a compressor that runs on gasoline, diesel, or electricity.
You may choose the ideal gas compressor for your application by being aware of these types and taking into account the important variables.
Keeping Your Gas Compressor Running Strong: Essential Maintenance Tips:
Gas compressor machine, which offer a dependable supply of compressed air, are the unsung heroes of many businesses. To guarantee a long lifespan and retain optimal performance, they need to have regular maintenance, just like any other diligent machine. The following are some vital pointers to maintain the smooth operation of your gas compressor:
- Oil Changes and Filter Replacements:
The lubrication and cooling of your gas compressor depends on clean oil, much like in your automobile. When it comes to oil changes, adhere to the manufacturer’s suggested timetable and use the right kind of oil for your particular compressor. Remember to change the oil filter concurrently to get rid of impurities that might damage internal parts.
- Cleaning of the Air Intake Filter:
To guarantee that pure air reaches the compressor, a clean air intake filter is essential. Airflow is restricted by a blocked filter, which lowers efficiency and makes the compressor work harder. As directed by the manufacturer, routinely check and clean the air intake filter. This little chore may prolong the life of your compressor and greatly enhance performance.
- Maintenance of the Cooling System:
To keep gas compressors from overheating, most of them have cooling systems. Usually, this system consists of an intercooler or radiator and fan. Check the cooling system often for accumulation of debris that might impede airflow. To enable ideal heat dissipation, make sure the fan blades spin freely and clean the radiator or intercooler fins.
- Frequent Inspections:
Inspect your compressor now, before a problem arises. To spot such problems early on, conduct routine inspections. Inspect for leaks around joints, loose fasteners, and indications of deterioration on belts or hoses. Timely resolution of small issues can save them from becoming more serious and requiring expensive repairs.
Listen for Warning Signs:
A well-maintained gas compressor should operate smoothly and silently. Pay attention to any warning signs. Vibrations or strange noises might be signs of an impending issue. Any variations in the compressor’s performance should be noted and dealt with right away. Seeking advice from a skilled expert is always a good idea if you anticipate a more serious problem.
Conclusion:
Working with a reputable manufacturer is crucial when choosing the best gas compressor machine for your requirements. When it comes to reliable, effective gas compressor solutions, LEIYAO Compressor stands out. With a dedication to innovation and top-notch customer support, LEIYAO gives you the confidence to confidently harness the force of compressed air.