Boost Efficiency & Profits: Choosing the Right Industrial Reciprocating Compressor
The Powerhouse of Industry: A Comprehensive Guide to Industrial Reciprocating Compressor
Numerous industrial processes depend on industrial reciprocating compressor as their workhorses. They are essential to many different processes, including the production of power, chemicals, and oil and gas. This thorough guide explores the world of industrial compressors, including its features, important selection criteria, and vital elements including price, upkeep, efficiency, and top manufacturers.
Understanding Industrial Reciprocating Compressors
Industrial reciprocating compressor are positive displacement devices that compress gas using a piston that moves inside a cylinder. Below is a summary of their main features:
- Working Principle:
Through an intake valve, low-pressure gas is drawn in by the piston as it travels back and forth inside the cylinder. After compressing the gas and raising its pressure, the piston pushes it out of a discharge valve.
- Variants:
Single-acting and double-acting variants are available for industrial compressors. While double-acting compressors produce compression on both the upward and downward strokes, providing better efficiency, single-acting compressors only compress gas on a single piston stroke.
- Stages:
Multi-stage reciprocating compressors are used in situations where extremely high discharge pressures are necessary. These types compress the gas gradually in several phases, cooling the gas in between to avoid dangerously high temperatures.
Applications: Areas of Excellence for Industrial Reciprocating Compressors
Industrial reciprocating compressor is employed in a variety of industries due to their adaptability, such as:
- Oil and gas:
Used in gas lift operations, wellhead gathering, and pipeline gearbox for natural gas compression.
- Chemical Processing:
Compressing different gases utilized in chemical industrial operations is done by chemical processing.
- Power generation:
Used in power plants to feed compressed air to combustion turbines.
- Food and Beverage:
Contribute to the food and beverage sector through applications and refrigeration systems.
- Manufacturing:
Used in a variety of manufacturing operations to supply power to pneumatic tools and equipment.
Factors to Consider When Choosing an Industrial Reciprocating Compressor
For optimum efficiency and effective operation, choosing the correct industrial reciprocating compressor is essential. Here are a few crucial things to think about:
- Application:
Knowing which particular gas is being compressed and what the necessary discharge pressure is crucial.
- Capacity:
The flow rate (CFM, or cubic feet per minute) of the compressor needs to be able to supply the air or gas that your application requires.
- Duty Cycle:
Select an appropriate duty cycle rating by taking into account the frequency and duration of compressor operation.
- Energy Efficiency:
If you want to reduce the amount of energy you use, look for compressors that have variable-speed drives.
- Maintenance requirements:
Set aside priority models with easily accessible parts for regular maintenance and easily obtainable spares.
Exploring Additional Considerations
- Industrial Compressor Duty Cycle:
Selecting a compressor that can meet your unique requirements requires an understanding of the duty cycle. Consult our compressor duty cycle guidance.
- Energy-Efficient Industrial Reciprocating Compressor:
In the modern industrial environment, energy efficiency is a crucial factor. Examine energy-saving techniques for reciprocating industrial compressors.
To save maintenance expenses and downtime, give low-maintenance compressors priority. Find out more about the maintenance schedules for industrial reciprocating compressors.
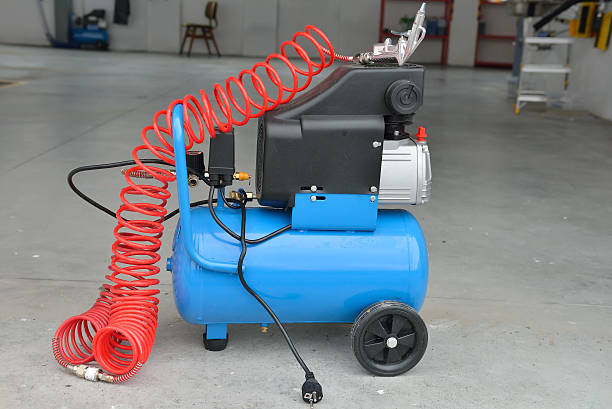
Industrial Reciprocating Compressor Cost
These reciprocating compressor’s price varies greatly based on several variables, such as:
- Size and Capacity:
Naturally, larger and more powerful compressors are more expensive.
- Features:
More expensive features include variable-speed drives, oil-free operation, and interstage cooling.
- Brand Reputation:
Compared to lesser-known manufacturers, premium brands with established reputations may fetch higher prices.
Energy-Efficient Industrial Reciprocating Compressors: Power Up Without Burning Out
Energy efficiency is becoming a need in today’s industrial environment, not just a nicety. Industrial reciprocating compressors can be an effective choice for applications that need compressed air. Their energy usage, nevertheless, can be substantial. To help you save money and lessen your environmental effects, this article examines characteristics and tactics to take into account when choosing an energy-efficient industrial reciprocating compressor.
Why Focus on Energy Efficiency?
The energy consumption of an industrial plant may be significantly influenced by industrial reciprocating compressors. This is why it’s so important to prioritize energy efficiency:
- Reduced Operating Costs:
You may save a lot of money on your power costs by using less energy.
- Environmental Sustainability:
You can help create a more sustainable organization and a smaller carbon imprint by using less energy.
- Government Incentives:
Purchasing energy-efficient industrial equipment can result in tax exemptions or refunds in several places.
Strategies for Energy-Efficient Operation
The following are some essential tactics to increase your industrial reciprocating compressor’s energy efficiency:
- Select the Correct Compressor Size:
You may avoid wasting energy by selecting a compressor whose capacity precisely fits the air demand of your application.
- Variable Speed Drives (VSD):
This technology eliminates energy loss during idle times by precisely adjusting the compressor’s motor speed to match varying air needs.
- Two-Stage Compression:
Two-stage compressors with interstage cooling are more energy-efficient than single-stage ones for high-pressure applications. By preventing significant heat accumulation, interstage cooling lowers the energy needed for compression.
- Appropriate Maintenance:
Preventive maintenance minimizes energy losses from wear and tear and guarantees peak performance. This covers routine air filter replacements, oil changes on schedule, and system maintenance.
- Leak Finding and Repair:
Energy efficiency may be greatly impacted by even little air leaks. Check for leaks in your compressed air system regularly, and fix any problems that are found right away.
Low-Maintenance Industrial Reciprocating Compressors: Keeping Your Operation Running Smoothly
Another crucial element in optimizing the performance and economy of your industrial compressor is minimizing maintenance needs. Here’s something to think about:
- Oil-Lubricated vs. Oil-Free:
Although oil changes are necessary for oil-lubricated compressors, these types are often more durable and efficient than oil-free ones. On the other hand, oil-free compressors remove the possibility of contaminating your compressed air system with oil.
- Simple Maintenance Access:
Select a compressor that has a design that makes it simple to reach vital parts like valves, drains, and filters. This lowers downtime and streamlines maintenance processes.
- Longer Service Intervals:
Seek for compressors that have longer service intervals between air filter replacements and oil changes. This results in reduced maintenance expenses and times.
Conclusion:
You may choose an industrial reciprocating compressor that provides ideal performance and minimizing your operational expenses. Leading brand of industrial reciprocating compressors that are low-maintenance and energy-efficient are available from LEiYAO Compressors. Get in touch with us right now to talk about your unique requirements and get the best solutions for your needs.