The benefits of rotary compressor
The Rotary Revolution: Understanding and Utilizing Rotary Compressor
The workhorses of the compressed air industry, these compressors are now a standard across many sectors. They effectively compress gas by a rotating action, in contrast to their reciprocating counterparts. This page explores the world of these compressors, including their varieties, uses, parts, upkeep requirements, and benefits over alternative compressor technologies.
A World of Designs: Unveiling the Different Types of Rotary Compressors
There are several designs of rotary compressor, each meeting a particular purpose. Here’s an overview of the most typical kinds:
- Screw Compressor:
The most popular type of rotary compressor, the screw compressor traps and compresses air using a set of interlocking males and female rotors. These rotors are perfect for applications needing constant pressure since they produce a constant airflow.
- Vane Compressor:
This type of compressor has a rotor with slots in it, and vanes slide inside the slots. The air that is trapped in the chambers is compressed by the vanes as the rotor rotates. Vane compressors are well-known for their low-pressure application adaptability and straightforward design.
- Scroll Compressor:
The Scroll Compressor is an inventive device that has two interlocking spiral scrolls that gradually trap and compress air pockets as it rotates. Scroll compressors are renowned for their excellent efficiency and silent operation.
Exposing the Uses: Areas in Which Rotary Compressors Thrive
Numerous applications in a wide range of sectors are powered by rotary compressor, the quiet workhorses of the compressed air industry. Rotary compressors are perfect for applications needing constant pressure since they provide a continuous stream of compressed air, in contrast to reciprocating compressors, which have a pulsing flow. Let’s examine a few of their most important uses:
- Powering Pneumatic equipment:
These compressors are the unsung heroes that power a plethora of pneumatic equipment, from the nail guns used to frame a house to the spray guns used to paint a car. These tools are utilized in manufacturing, automotive repair, and construction, and their capacity to provide a constant supply of compressed air guarantees smooth operation and reliable outcomes.
- The Cool Option for Air Conditioning and Refrigeration:
For both home and commercial refrigeration and air conditioning systems, a rotary compressor is a common option. Improved system performance is a result of their effective design and capacity to manage refrigerants. This results in both effective food preservation in business settings and a colder, cosier atmosphere at home.
- Industrial Procedures: Inhaling Pressurized Air:
These compressors are essential to many different industrial operations; they are not merely for comfort. They provide precise power to pneumatic actuators that automate industrial processes and enable a variety of chemical reactions that need constant pressure. The hidden engine underlying many industrial applications is the rotary compressor, whether it be used in the production of plastic bottles or the processing of chemicals.
Apart from these well-known uses, rotary compressors are employed in numerous other industries, such as:
- Medical & dentistry Equipment:
Their quiet operation and steady airflow make them a good choice for these delicate environments, whether they are powering dentistry drills or running medical equipment.
- Food & Beverage Processing:
To guarantee constant pressure and high-quality product throughout procedures like bottling and packing, rotary compressors are employed in this sector.
We can better appreciate these compressors’ influence on both industrial processes and our daily lives if we are aware of their wide range of uses. These compressors quietly shape the world around us, doing everything from keeping us cool to powering tools and enabling industrial production.
Under the Hood: Exploring the Components of a Rotary Compressor
Numerous industries rely on rotary compressors as their workhorses due to their efficient operation and constant airflow. What, though, gives them their tick? Now let’s examine the essential elements that manage the compression process:
- The Heart of the Action:
The Screw and Scroll Compressor Rotors are in the centre of the action. The main attraction is these intermeshing rotors. Scroll compressors use two interleaving spirals to trap air, whereas screw compressors use a male and female rotor working together. These rotors produce air pockets that compress more and more as they spin.
- The Vane Compressors, often known as the Guardians of Flow:
These aren’t superheroes in vane compressors, but they are still essential parts. A slotted rotor houses these sliding vanes. The air that is trapped in the chambers is compressed by the vanes as the rotor rotates.
- Maintaining Smooth Function:
Bearings Consider a ballet: the rotors must move fluidly and effectively. Bearings serve as the compressor’s silent supporters, reducing friction and guaranteeing that the spinning parts run smoothly.
- Closing the Deal: Seals:
A compressor’s deadliest enemy may be leaks. Seals are essential for preserving pressure integrity, maximizing performance, and preventing leaks between the compressor’s compression chamber and other components.
- The Lifeline of Lubrication for Oil-injected Compressors:
Oil is used by certain rotary compressors for purposes other than cooking! Lubricating surfaces with oil lessens wear and friction between moving elements. Additionally, it helps to keep the compressor cool and running efficiently. (Remember that frequent oil changes are crucial for oil-injected compressors!)
- The Engine of Power: Drive System:
A power source is necessary for any machine. The compressor components rotate due to the power provided by the drive system, which can be a motor, belt, or other mechanism. This rotation initiates the compression process.
Gaining knowledge of these essential parts and their functions helps you have a greater grasp of the complex mechanism that powers a rotary compressor. This well-oiled machine guarantees effective compressed air delivery, fuelling a myriad of everyday uses.
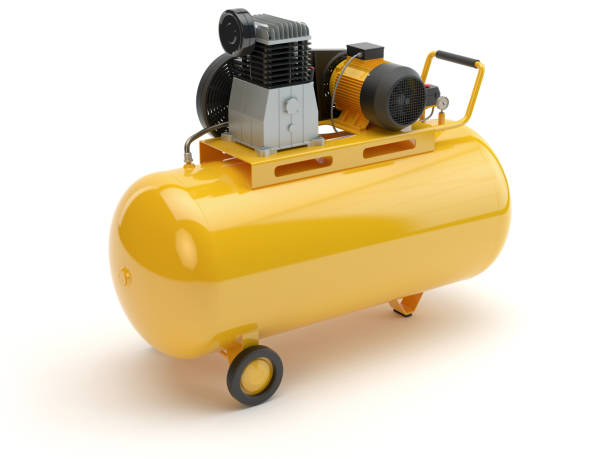
Sustaining Maximum Efficiency: An Overview of Rotating Compressor Upkeep
These compressor needs regular maintenance to guarantee smooth operation, lifespan, and peak performance, just like any other demanding machinery. Here is a summary of essential procedures to maintain the optimal performance of your rotary compressor:
- Oil Changes are Essential:
For oil-injected compressors, oil changes are crucial. The vital component of an oil-injected rotary compressor is oil. Frequent oil changes keep the engine properly lubricated and reduce friction between moving parts by removing impurities that accumulate during operation. Don’t ignore this important assignment! See the manual for your compressor to find out how often to change the oil. Ignoring oil changes can result in more wear and tear, which reduces longevity and performance.
- Don’t Forget the Filters:
The interior components of your compressor are safeguarded by the air intake filters. They guard against debris, dust, and filth getting inside the system, which could harm it and impair its functionality. Replace air filters regularly according to the manufacturer’s recommendations. Restricting airflow and decreasing efficiency due to clogged filters necessitates frequent filter changes for optimal performance.
- Examination and Cleaning:
Although rotary compressor requires less maintenance than reciprocating ones in general, routine examination and cleaning can help avoid problems with performance. If you’re unsure about the frequency or particular components to inspect, go to the manufacturer’s instructions. This may entail looking for wear or accumulation on the air intake and discharge valves. Maintaining optimal performance can be facilitated by routine cleaning of these components.
- Performance monitoring:
Preventive maintenance is essential! Keep a close eye on important performance metrics such as vibration levels, air temperature, and discharge pressure. Any departure from standard operating parameters should be detected as soon as possible to avoid more serious issues later on. To make this process easier, the majority of rotary compressors are fitted with gauges or monitoring systems.
The Benefits of Rotary Technology: Why Select a Rotary Compressor?
These are dependable and effective workhorses in the compressed air industry. But why are they better than other types of compressors, especially reciprocating compressors? Let’s examine the main benefits that have strengthened their position in a variety of industries:
These compressors provide a constant stream of compressed air, in contrast to reciprocating compressors, which have a pulsing flow. Because of this, they are perfect for uses that need constant pressure, such as operating pneumatic tools or preserving exact pressure during industrial operations. In these applications, the constant flow results in more efficient and seamless operation.
- A Calmer Operation: A Welcome Harmony:
In many businesses, noise pollution can be a hazard. When opposed to reciprocating compressors, rotary compressors often run at much lower noise levels. In some situations, this quieter operation can even meet with higher noise laws, making the workplace more comfortable.
- Efficiency Is Everything: Conserving Energy and Money
When it comes to efficiency, rotary compressors are preferable to reciprocating equivalents. Their layout reduces energy loss, which lowers operational expenses. This results in long-term significant energy savings for companies and industries with large compressed air demands.
- Lower Maintenance Requirements: Increased Productivity, Less Downtime
When opposed to reciprocating compressors, these compressors often require less regular maintenance due to their simpler construction. This means that you will have less downtime for repairs and maintenance, freeing you up to concentrate on your main company operations.
- A Trace for Every Requirement Size Counts:
Compared to reciprocating compressors, these compressors are available in a greater variety of sizes and designs. This gives you additional options for selecting a compressor that best fits your needs for compressed air and space limits. There is a rotary compressor that is suitable for any kind of application, be it a tiny workshop or an industrial complex requiring a larger model.
Conclusion:
Prepared to use rotary compressor to their full potential? Examine the extensive range of LEIYAO Compressor available. To meet your needs and price range, we provide a range of models. See which rotary compressor will be best for you to further your tasks by visiting our website now!