Industrial Air Compressor Applications: Powering Your Industry
The Industrial Powerhouse: An All-Inclusive Guide to Industrial Air Compressor
The noises of industrial growth are the unceasing buzz of machinery and the rhythmic clatter of tools. But the industrial air compressor is the unsung hero that often goes unnoticed beneath this cacophony of activity. This industrial marvel, which powers everything from paint sprayers in body shops to pneumatic tools on assembly lines, is the lifeblood of many processes.
This thorough book delves deeply into the world of these air compressors, examining their various varieties, features, uses, and important factors to take into account when selecting the best one for your particular requirements. By the time it’s all over, you’ll know everything there is to know about these vital pieces of machinery and how they help many industries run smoothly.
The Fundamental Technology: Exposing Various Industrial Air Compressor Types
There are several types of industrial air compressor, each designed to meet the demands of a particular application and pressure level. The most prevalent kinds are broken down as follows:
- Reciprocating Industrial Air Compressor:
In this conventional configuration, air is compressed by a piston that moves inside a cylinder. These compressors are appropriate for a range of applications because of their straightforward and dependable design. Nevertheless, in comparison to certain contemporary solutions, they might need more upkeep.
- Screw Industrial Air Compressor:
This cutting-edge design compresses air using helical screws that are intermeshed. Compared to reciprocating types, screw compressors provide constant airflow, smoother operation, and higher efficiency. They are a popular option for many industrial applications since they are also often quieter and require less maintenance.
- Centrifugal Industrial Air Compressor:
To raise air pressure, these high-speed compressors use revolving impellers. When high flow rates are needed in large-volume, continuous-duty applications, centrifugal compressors are the best choice. They might not be appropriate, therefore, in circumstances requiring extremely high discharge pressures.
Beyond the Basics: Key Components of an Industrial Air Compressor System
Gaining knowledge of the essential elements of an industrial air compressor system enhances one’s comprehension of its operation:
- Air Intake Filter:
This part keeps the compressor safe by filtering impurities, dust, and debris out of the entering air stream.
- Air Compressor Unit:
The system’s central component, the air compressor unit, uses screws, pistons, or impellers, depending on the kind of compressor, to compress air.
- Air Compressor Tank:
This pressurized container holds compressed air, serving as a buffer and guaranteeing a steady supply for a range of uses.
- Aftercooler:
Heat is produced during air compression. A key component in lowering this heat is the aftercooler, which is frequently a heat exchanger that uses air or water. Reducing the temperature guarantees effective functioning and increases the system’s longevity.
- Oil-Lubricated Compressors:
The separator in these compressors eliminates oil mist from the compressed air stream, providing purer air for applications that demand it.
- Air Dryer (Optional):
By eliminating moisture from compressed air, an air dryer helps to maintain constant performance and avoid corrosion in downstream equipment.
- Air Pressure Regulator:
This part controls the compressed air’s output pressure, enabling users to tailor it to the demands of particular applications.
- Drain Valve:
Condensate, or water, that builds up in the air tank and other parts can be removed thanks to the drain valve.
- Safety Relief Valve:
An essential safety device, it releases pressure automatically if it rises above safe levels, preventing possible harm to the system.
Choosing the Appropriate Industrial Air Compressor: The Power of Choice
There is no one-size-fits-all solution when it comes to selecting the ideal industrial air compressor. Take into consideration these important elements to guarantee peak performance and efficiency for your particular needs:
- Airflow Rate (CFM):
The amount of compressed air that is delivered per minute is measured by the airflow rate (CFM) meter. A compressor’s CFM should be matched to the air demand of your applications. Similar to water flow, higher CFM is needed for high-pressure jobs like sandblasting than for low-pressure tasks like tyre inflation.
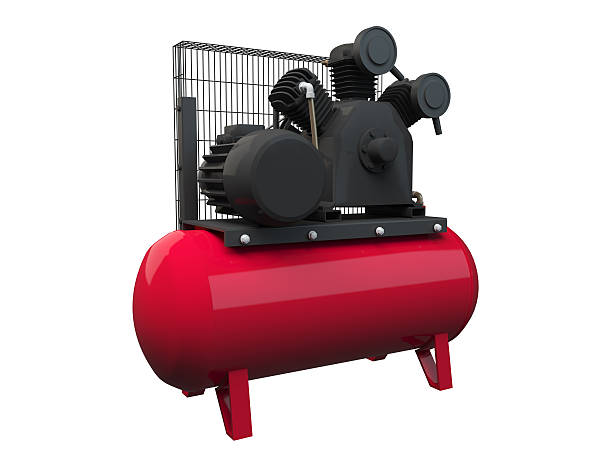
- Discharge Pressure (PSI):
The air pressure needed for a given application varies. While operating a large sandblaster may require 120 PSI or more, nail guns may operate at 70 PSI. Selecting a compressor that has enough discharge pressure will guarantee that your tools work well.
- Duty Cycle:
Take into account the frequency of operation of your compressor. To power a production line or other continuous duties, a heavy-duty compressor that is meant for prolonged usage is essential. In certain situations, such as sporadic use in a repair shop, a lighter-duty model could be adequate.
- Power Source:
Diesel, gasoline, and electricity are the available power sources for industrial air compressors. Electric variants are perfect for buildings with dependable power systems because they operate cleanly. Compressors for gasoline and diesel are portable and ideal for use in isolated areas or in applications that need mobility.
- Requirements for Air Quality:
To avoid contamination, many applications require compressed air that is free of oil. In general, oil-lubricated compressors are more economical and efficient in situations where oil mist is not a concern. Cleaner air is provided by oil-free compressors, but they may initially cost more.
The Applications: Where Industrial Air Compressors Reign Supreme
The silent workhorses propelling various industries forward are these air compressors. Because of their capacity to produce pressured air, they are vital for a wide range of applications, including:
- Industrial Manufacturing:
Pneumatic instruments like impact drivers, wrenches, and drills are powered by air compressors, which keep assembly lines humming with activity. Industrial air compressors guarantee efficient and seamless assembly procedures in the production of furniture and automobiles alike.
- Construction:
Industrial air compressor plays a critical role on construction sites, from framing houses to destroying buildings. Compressed air powers staple guns, concrete breakers, and nail guns, facilitating productive construction work. They are also employed in paint peeling, sandblasting, and heavy machinery tyre inflation.
- Food and Beverage Processing:
For several procedures involved in the creation of food and beverages, it is essential to maintain constant air pressure. Air compressors are employed in mixing apparatus operation, ingredient flow management, and bottling and canning lines. To stop spoiling, sterile air is sometimes used during packaging.
- Energy and Power Generation:
An essential component of the energy industry is these air compressors. They power pneumatic equipment used in power plant maintenance, operate cooling system valves, and even help in the production of wind turbine blades.
- Chemical Processing:
Chemical facilities use a lot of compressed air for a variety of reasons. It facilitates the movement of materials and liquids, controls valves and actuators, and supports the drying and cleaning processes. Safe and effective chemical manufacturing is ensured by the accurate management of air pressure.
- Many More:
These compressors’ applications go well beyond these basic illustrations. They are used in many different industries, including mining, oil and gas exploration, auto repair, and the operation of dental and medical equipment. They are essential to contemporary industrial processes because of their dependability and adaptability. You will have a better knowledge of the wide range of uses for these air compressors and how they have shaped our world.
The Power of Efficiency: Unveiling the Benefits of Industrial Air Compressors
In the realm of industry, efficiency is king. These air compressors pack a powerful two-fold punch by maximizing efficiency for a range of applications and supplying the power of compressed air. Here are some of the main advantages that make them essential across a wide range of industries:
- Increased Productivity:
Compared to manual methods, air compressors provide workers with pneumatic equipment that expedites activities. Compressed air tools shorten production cycles, which boost productivity and profitability. Examples of these cycles include quick assembly using impact wrenches and effective drilling and riveting.
- Decreased Costs:
These compressors have major long-term cost benefits, despite their initial seemingly large expenditure. Compared to certain electric or hydraulic tools, their robustness and dependability reduce downtime and maintenance requirements. Their energy-efficient models can also drastically lower your energy usage.
- Versatility Unbound:
The variety of uses for industrial air compressors is what makes them so beautiful. Many different tools and pieces of equipment can be powered by a single compressor, doing away with the need for several separate power sources. This adaptability results in a work atmosphere that is more fluid and dynamic.
- Increased Safety:
Pneumatic tools driven by compressed air have inherent safety benefits over traditional equipment powered by electricity or combustion engines. For instance, they are safer to use in flammable areas because they don’t spark easily.
- Clean Operation:
For applications requiring clean air, modern oil-free air compressors provide a major benefit. They are perfect for jobs like food and beverage processing, electronics manufacturing, and pharmaceutical production since they remove the possibility of oil contamination.
- Consistent Performance:
Your tools and equipment will operate consistently thanks to industrial air compressors, which are made to produce a steady stream of compressed air. This reduces the possibility of disruptions or discrepancies during crucial processes and results in predictable workflows.
Conclusion:
You can make an informed decision that maximizes the purchase of an industrial air compressor by carefully weighing aspects. Never be afraid to seek professional assistance in choosing the ideal model for your particular requirements by speaking with a reputable industrial air compressor supplier like LEIYAO Compressor.