Air Compressor Piston Seal: The Complete Guide
The Essential Guide to Air Compressor Piston Seals:
Maintaining the different parts of your air compressor is necessary to keep it operating properly, and the piston seal is one of the most important parts. This thorough book delves deeply into the topic of air compressor piston seal, covering everything from how they work to frequent problems and how to solve them. This article gives you the expertise to make sure your air compressor runs as efficiently as possible, regardless of whether you’re a seasoned professional or a do-it-yourselfer.
Understanding Air Compressor Piston Seals:
Although your air compressor may appear to be a strong device, its effectiveness is dependent on a small but vital part called the piston seal.
- To keep compressed air from leaking back into the crankcase, this unsung hero creates a tight seal between the piston and cylinder wall. Consider it as a gatekeeper, making sure that the greatest amount of pressure is applied to your instrument.
- Reduced air pressure, increased oil consumption, strange sounds, and obvious wear on the seal itself are all indicators that a piston seal is deteriorating.
- For the best air compressor performance, don’t be afraid to investigate more into troubleshooting or replace the seal if you have any suspicions.
The Seal Deal: Exploring Different Air Compressor Piston Seal Options:
The cylinder is where your air compressor performs most of its work, and the piston seal is an important component of this process. These inconspicuous rings serve as an essential seal, keeping compressed air from re-entering the crankcase. However, not every piston seal is made equally. Selecting the best kind for your air compressor needs will be made easier if you are aware of the many available varieties and their advantages.
- The PTFE Champion:
Teflon, also known as polytetrafluoroethylene (PTFE), is the substance with the highest wear resistance. PTFE seals are perfect for heavy-duty jobs because they perform well in situations that call for prolonged use and high temperatures. Their low coefficient of friction reduces drag on the piston, enhancing the compressor’s overall efficiency.
- Polyurethane:
This adaptable material conforms nicely to the cylinder wall in a variety of air compressor types thanks to its exceptional flexibility. For general-purpose applications, polyurethane seals are a desirable option since they offer a dependable seal under moderate operating temperatures and conditions. Under extremely high temperatures or workloads, they could not hold up as well as PTFE seals.
Beyond the Binary:
The most used materials are these two, although there are other possibilities as well, such as filled PTFE, which is PTFE combined with fillers like carbon or fiberglass for improved performance in particular applications.
Choosing Your Champion:
Several elements determine which piston seal is best for your air compressor. Take into account the working temperature, workload level, and the recommended model for your air compressor. You may choose the best type of seal for lifespan and performance by consulting the instructions that came with your air compressor or by consulting a trained technician.
When to Consider Replacing Your Air Compressor Piston Seal?
There are a few indicators that the air compressor piston seal needs to be replaced:
- Decreased Air Pressure:
One of the most obvious signs of a worn or broken piston seal is a discernible decline in air pressure production.
- Overconsumption of Oil:
Leaking seals may permit oil to enter the compressed air chamber, which might contaminate your tools and result in excessive oil consumption.
- Unusual Noises:
When a piston seal fails, it may make strange noises like rattling or knocking while the machine is operating.
- Visible Wear and Tear:
The state of the seal may be determined by looking for cracks, rips, or an excessive amount of hardening.
How to Replace a Piston Seal on an Air Compressor?
Although changing a piston seal may appear difficult, DIY enthusiasts with any mechanical understanding can usually do the process with ease. Below is a broad summary of the procedure:
- Drain the Compressor Oil:
Find the oil drain plug and empty the used oil into the pan to empty the compressor’s oil.
- Dismantle the Compressor:
By the instructions provided in your air compressor’s handbook, remove the pertinent parts to get to the cylinder and piston. This could entail taking off the connecting rod, the cylinder head, and the valve covers.
- Discard the previous piston seal:
Using a screwdriver or seal removal tool, carefully remove the old, worn-out piston seal, taking care not to harm the cylinder wall.
- Clean the Cylinder Wall:
Use a clean cloth to wipe away any dirt or leftover oil.
- Put the New Piston Seal in Place:
For accurate installation, see the new seal kit instructions. The seal will usually stretch to a tight fit around the piston groove.
- Reassemble the Compressor:
Gently put the dismantled parts back together in the correct sequence, being sure to tighten the bolts to the recommended torque.
- Fill up with Fresh Oil:
As directed in the instruction booklet that came with your air compressor, add new oil.
Taming the Leaks: Troubleshooting Air Compressor Piston Seal Issues:
Smooth operation and maximum performance are directly correlated with a healthy air compressor piston seal. But issues can arise with even the strongest seal. Here are some frequent problems with air compressor piston seals and how to fix them:
- The Enduring Breach:
A worn-out or damaged seal is often indicated by a continuous air leak around the piston seal region. The best remedy is to replace the seal. Make sure the new seal kit you use fits the model of your air compressor.
- On the Decline: Performance
Decreased air pressure and a general decline in performance may indicate a failed piston seal. Examine the seal for indications of wear and replace it if required. Recall that a damaged seal prevents compressed air from escaping back into the crankcase, which reduces the power your air compressor can produce.
- Unexpected Places for Oil:
The compressed air may become contaminated by oil due to leaky seals. This puts your pneumatic tools in danger in addition to lowering performance. To reduce future oil contamination, take care of the seal problem and think about utilizing an air-oil separator.
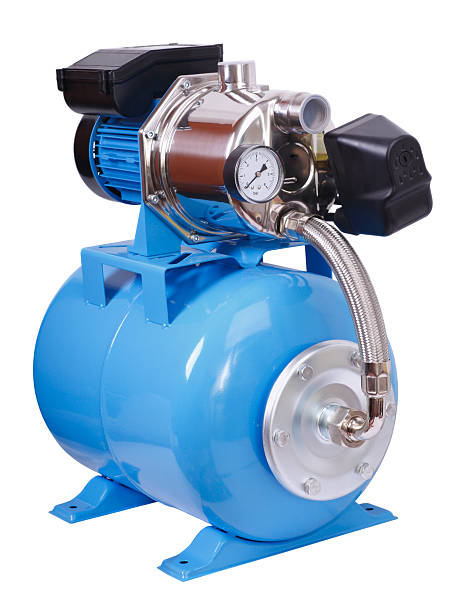
When the Heat is On Choosing the Best High-Temperature Air Compressor Piston Seal:
Particular care must be taken with air compressors operating in hot conditions, particularly about the piston seal. Since this important part bears the brunt of the heat, selecting the appropriate material is essential to preserving performance and avoiding premature wear.
The High-Temperature Hero: PTFE Takes the Stage
The best material for withstanding high temperatures is polytetrafluoroethylene (PTFE). PTFE, sometimes referred to as Teflon, has outstanding heat stability. It can withstand high temperatures without cracking or losing its ability to seal. For air compressors utilized in hot conditions such as foundries, asphalt paving, or even desert areas, this makes it the best option.
Beyond the Basic PTFE:
Even while PTFE which is normal offers excellent heat resistance, certain applications can need even more. The use of filled PTFE goes one step further. These sealants improve particular qualities by adding fillers like carbon or fiberglass. For example, in addition to its high-temperature capabilities, carbon-filled PTFE provides enhanced wear resistance.
Matching the Material to the Need:
Even though PTFE is the preferred material for high-temperature applications, it’s crucial to take other aspects into account than heat. The best option may vary depending on the particular operating conditions, workload level, and air compressor model. You may choose the best material for your particular requirements by consulting the handbook that came with your air compressor or hiring a trained technician, which will ensure high-temperature resistance and excellent performance.
Utilizing the Piston Seal in Air Compressors:
The piston seal is the hero at the center of your air compressor. This straightforward ring is essential to maintaining optimal performance and seamless functioning. But how precisely does it work?
A tight barrier is created between the piston and the cylinder wall by the air compressor piston seal. Think of it like a gatekeeper. The seal keeps pressurized air from leaking back into the crankcase when the piston travels back and forth inside the cylinder. This guarantees that all of the pressure that is produced is directed toward the outlet, which will power your pneumatic equipment in the end.
Beyond Basic Function:
The piston seal has uses that go beyond just stopping leakage. They further support:
- Maintaining Efficiency:
The seal makes sure that your tools receive the greatest pressure possible by reducing air leakage, which maximizes productivity and reduces energy loss.
- Minimizing Friction:
By enabling smooth piston movement inside the cylinder, low-friction materials such as PTFE lessen wear and tear on the cylinder wall and piston.
- Safeguarding Internal Components:
The seal keeps oil out of the compressed air chamber, preventing oil contamination of your instruments.
Conclusion:
LEIYAO Compressor is your trustworthy partner for all of your air compressor piston seal needs. We provide a large assortment of premium piston seals that work with different air compressor types. To locate the ideal replacement seal for your air compressor and maintain the smooth operation of your tools, visit our website or get in touch with us right now!