Industrial Workhorses: Single Stage Double Acting Reciprocating Compressor in Action
Single Stage Double Acting Reciprocating Compressors: Powerhouse of Performance
Compressed air and gas are essential in the field of industrial applications for many uses. The single stage double acting reciprocating compressor is one of the workhorses that must efficiently provide this compressed energy. This article is an invaluable resource for prospective purchasers, engineers, and everyone else interested in the field of industrial gas compression since it explores the inner workings, uses, and benefits of this strong equipment.
Understanding the Design: Single Stage vs. Double Acting
One cylinder is used for the compression process, which is referred to as a single stage. In one piston stroke, the gas or air is brought in, compressed, and released. When it comes to the piston itself, double acting is involved. A double-acting design uses both sides of the piston to compress the gas, in contrast to single-acting compressors that only use one side. The amount of compressed gas flowing every crankshaft rotation is greatly increased as a result.
Highlighting Functionality: Power, Flow, and Durability of single stage double acting reciprocating compressor
- High-volume, single-stage compressor:
Within a single stage arrangement, the double-acting design intrinsically provides a larger flow rate than its single-acting equivalents. Because of this, they are perfect for applications that need a steady supply of compressed gas or air.
- High-pressure single stage compressor:
Depending on the application, single stage compressors can attain greater pressures. Although they are typically designed for lower to moderate pressure applications, certain versions can reach higher pressures.
- Continuous duty compressor:
Double-acting reciprocating compressors are a good choice for continuous operation in harsh industrial settings because of their sturdy construction. Long-term dependable functioning is ensured by their durability.
Applications: Where Single Stage Double Acting Compressors Shine?
The most popular use for single stage double acting reciprocating compressors is in industrial reciprocating compressors. A double acting reciprocating compressor might be the key to increasing productivity and streamlining operations whether you are in manufacturing, oil and gas, air separation, or another sector.They are employed in some industrial industries, such as:
- Manufacturing:
Providing compressed air to run machines, operate pneumatic tools, and regulate procedures.
- Chemical processing:
Chemical processing is the process of moving, reacting, and separating chemicals at different phases of the chemical manufacturing process.
- Oil and gas:
Used for operations such as instrument air supply, pipeline injection, and wellhead gas collecting.
- Air separation:
Compressed air can be produced in the first phases of air separation facilities to separate it further into nitrogen and oxygen. An article specifically for air separation compressors might be helpful, much like the ones about oil and gas.
Making the Choice: Single Stage vs. Double Stage Compressors:
Although single-stage double-acting compressors provide several benefits, it’s important to know the distinction between single- and double-stage compression. The air or gas is compressed to its final pressure in a single step using a single stage compressor. On the other hand, a twin stage compressor achieves greater end discharge pressures by compressing the gas twice.
Beyond Functionality: Advantages of Single Stage Double Acting Compressors
Although delivering compressed air or gas is the primary purpose of a single stage double acting reciprocating compressor, there are many more advantages to using one than just doing the task at hand. They are an in-depth examination of the benefits that make these compressors a well-liked option for a range of industrial applications.
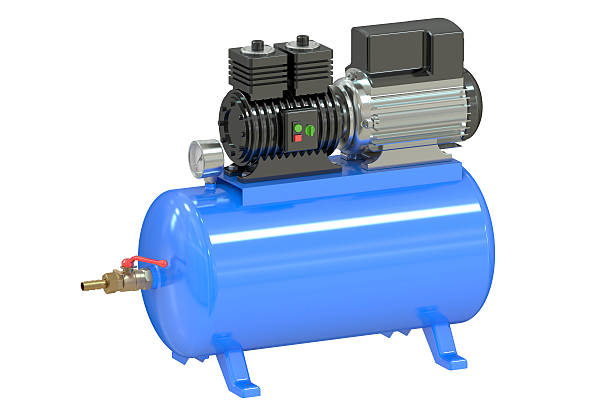
- Enhanced Efficiency and Productivity:
High Flow Rate: Compared to single-acting compressors operating in a single stage arrangement, the double-acting design’s ability to compress on both piston strokes results in a notable increase in flow rate. This results in increased productivity overall and in job completion times for applications requiring a steady stream of compressed air at high volumes.
Decreased Downtime: These compressors’ strong construction and exceptional durability reduce the need for regular maintenance and repairs, which reduces downtime and boosts operating effectiveness.
- Cost-Effectiveness:
Lower Initial Investment: Single stage double acting systems are often less expensive upfront as compared to double-stage compressors delivering comparable flow rates. This makes them an affordable alternative for companies searching for a compressor that is both potent and reasonably priced.
Simplified Maintenance: The established and uncomplicated design makes maintenance simpler, which lowers labor expenses and eliminates the need for specialist personnel. Further reducing expenses is the great durability, which also reduces the frequency of necessary maintenance.
- Versatility:
Depending on the particular model, single stage double acting compressors may generate a high flow rate at moderate pressure levels, making them suitable for a wide range of industrial applications. Because of their adaptability, they are a great resource for businesses with a range of compressed air or gas requirements.
- Dependability:
Even in harsh industrial settings, dependable functioning is guaranteed by the sturdy structure and tried-and-true design. You can rely on these compressors to operate consistently for lengthy periods.
- Compact Footprint:
Single stage double acting designs have the potential to be more compact than certain other compressor types. When there is a shortage of room, this might be a big benefit.
- Environmental Considerations:
Decreased Energy Consumption: When producing the same flow rate, single stage double acting compressors may use less energy than certain other compressor alternatives because of their innate efficiency. This results in less operational expenses and a smaller environmental impact.
Durability and Longevity: These compressors have a long lifespan that reduces the need for regular replacements, which can help to reduce their total environmental effect.
Conclusion:
A variety of industrial compressed air and gas requirements can be effectively addressed by a single stage double acting reciprocating compressor. Businesses looking for dependable and potent performance will find them to be a great asset because of their strong design, cost-effectiveness, and capacity to offer high flow rates at moderate pressures. LEiYAO Compressors provides our global customers with all-inclusive, one-stop solutions while guaranteeing great product quality and first-rate service.