Natural Gas Reciprocating Compressor: The Workhorse of the Industry
What is a natural gas reciprocating compressor?
A workhorse device that is widely used in the natural gas industry is a natural gas reciprocating compressor. It works similarly to a strong pump that was made especially to raise natural gas pressure. This compressed gas is essential for several natural gas-related processes, including residential electricity and extraction wells. The reciprocating compressor is a crucial piece of equipment used in the natural gas sector. From the wellhead to the customer, these devices are essential to the natural gas life cycle at different points.
The Powerhouse behind natural gas applications:
Reciprocating compressors are positive displacement devices that raise natural gas pressure using pistons that are movable within cylinders. The natural gas industry then uses this pressured gas for several purposes, including:
- Natural Gas Pipeline Boosting:
Friction causes pressure decreases that are inevitable when natural gas travels large distances through pipelines. To increase pressure and guarantee effective gas supply to customers, reciprocating compressors are positioned strategically along pipelines.
- Production of Compressed Natural Gas (CNG):
Compared to conventional fuels for automobiles, compressed natural gas (CNG) burns cleaner. Natural gas can be efficiently stored and transferred in CNG cars because of the high pressure at which reciprocating compressors compress it. This is why reciprocating compressors are essential to the manufacture of CNG.
- Gathering and Processing Gas:
Natural gas frequently contains contaminants such as water vapor and other hydrocarbons once it is extracted from wells. In gas collection and processing facilities, reciprocating compressors are used to remove these undesirable components, producing cleaner, higher-quality natural gas that can be distributed and transported further.
- Reinjection in the Production of Oil and Gas:
Some natural gas becomes trapped underground alongside the oil during the extraction of oil and gas. This natural gas may be reinjected into the reservoir using reciprocating compressors, improving oil recovery and optimizing resource usage.
- Wellbore Cleanup:
To get rid of debris and formation fluids, wellbore cleanup is crucial after well drilling. The pressure required to help with this process may be supplied by reciprocating compressors, guaranteeing a wellbore that is clean and functional. Visit our website to see our extensive selection of reciprocating compressors that are appropriate for a variety of applications.
The Building Blocks of a Reciprocating Compressor:
To fully appreciate the operation of a reciprocating compressor, one must comprehend its basic parts:
- Stages of a Reciprocating Compressor:
Single-stage and multi-stage designs are possible for reciprocating compressors. While multi-stage compressors get greater discharge pressures by compressing the gas in stages and intercooling between stages for enhanced efficiency, single-stage compressors boost pressure all at once.
- Piston Rod Packing:
The piston rod serves as a link between the crankshaft and the piston inside the cylinder. Gas leakage between the cylinder and crankcase is reduced by efficient piston rod packing, guaranteeing peak compressor performance.
- Design of the Crosshead:
The crosshead is the part that joins the connecting rod and piston rod. It lessens wear and friction on the cylinder walls by directing the piston rod in a straight path.
- Interstage Coolers:
Heat exchangers that remove heat produced during compression between stages are known as interstage coolers in multi-stage compressors. In addition to preventing overheating, this cooling procedure increases compressor efficiency overall.
- Lubricating a reciprocating compressor:
These reciprocating compressors are essential to lowering wear and friction inside the device. Forcible lubrication systems are commonly employed by reciprocating compressors to guarantee sufficient lubrication of all moving components.
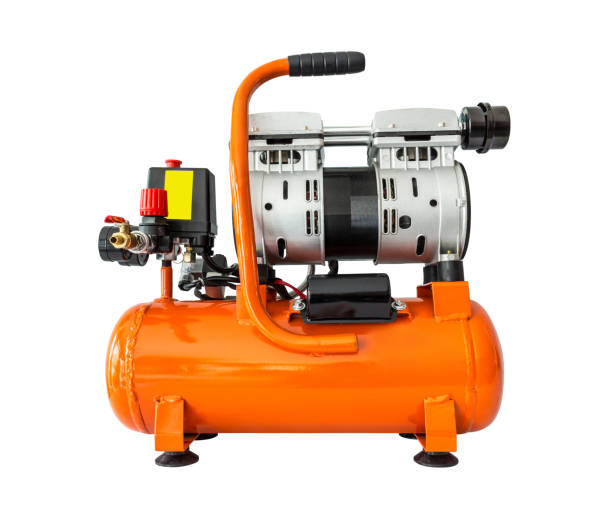
Performance and Efficiency: Metrics that Matter
It’s crucial to comprehend the performance and efficiency parameters of a natural gas reciprocating compressor before choosing one:
- Horsepower (hp) of a reciprocating compressor:
Horsepower (hp) is a measure of the power required for a compressor to run. A compressor that has the right horsepower will be able to manage the pressure and flow rate needed for your particular application.
- Discharge Pressure:
The pressure at which compressed gas leaves the compressor is known as the discharge pressure. The downstream application’s particular pressure requirements must be satisfied by this parameter.
- Volumetric Efficiency:
Volumetric efficiency gauges how well a compressor retains and condenses gas with each intake stroke. Reduced gas loss and enhanced compressor performance are directly correlated with increased volumetric efficiency.
- Brake Specific Fuel Consumption (BSFC):
The Brake Specific Fuel Consumption (BSFC) statistic is used to determine how fuel-efficient a compressor is. Lower operating costs and improved fuel economy are indicated by a lower BSFC.
Keeping Your Compressor Running Smoothly: Maintenance Considerations
Here’s a thorough analysis of reciprocating compressor maintenance factors that builds on the preceding section:
Scheduled checks: Qualified technicians conduct routinely scheduled checks to help detect possible problems early on and avoid expensive failures and downtime. Usually, these examinations entail:
- Examining the condition and amount of lubrication.
- Checking the wear and leaks in the piston rod packing.
- Ensuring that valves are operating properly.
- Keeping an eye on the cleanliness of the air intake filters.
- Checking the operation of the cooling system.
Oil and Filter Changes:
To keep your lubricant at its best and get rid of any pollutants that build up over time, oil changes are essential. The particular compressor model and operating circumstances determine how often an oil change is necessary. Similar to this, to guarantee that clean air reaches the compressor, air intake filters need to be changed regularly.
Monitoring Performance Parameters:
Keep a careful eye on important performance indicators like as vibration levels, horsepower usage, and discharge pressure. Deviations from the typical operating range may be a sign of possible issues that need to be addressed.
Leaks Should Be Fixed Right Away:
Gas leaks might provide safety risks in addition to performance issues. Any leaks that are found should be fixed right away by professionals.
Conclusion:
LEiYAO Compressors global commercial reach extends to more than 20 nations and areas. 500 committed workers on our team have a positive impact on our dynamic operations.