Large Reciprocating Compressors Not Working? Here’s Why!
The Powerhouse of Industry: Large Reciprocating Compressors Explained
Large reciprocating compressors provide high-pressure air for a variety of demanding applications. They are the workhorses of innumerable industrial operations. Their dependability and effectiveness make them an essential component in many industries, ranging from air separation units and natural gas transportation to oil refineries and chemical facilities. However, to guarantee peak performance, appropriate upkeep, skill in repairs, and a solid grasp of their uses are necessary. This in-depth manual explores the world of big reciprocating compressors, including their uses, servicing and maintenance procedures, and important factors to take into account when selecting the appropriate model.
Understanding the Power Behind the Pressure: Working Principle of Large Reciprocating Compressors
Fundamentally, a large reciprocating compressors functions using the same idea as its smaller equivalents. Below is a summary of the main parts and how they work:
- Electric motor or heavy-duty engine:
Provides the compressor’s power.
- Crankshaft:
Produces a reciprocating (back-and-forth) action from the motor or engine’s rotating motion.
- Connecting Rod:
The connecting rod transfers the reciprocating action from the crankshaft to the piston.
- Piston:
Air is drawn in during the intake stroke and compressed during the discharge stroke by a piston that travels inside a cylindrical chamber, or cylinder.
- Inlet Valve:
Air can enter the cylinder during the intake stroke thanks to the intake valve.
- Outlet Valve:
During the discharge stroke, the outlet valve allows pressurized air to leave the cylinder and enter the discharge line.
- Cooling System:
Uses water or oil coolers to control the heat produced during operation.
- Intercoolers:
Cool compressed air in multi-stage compressors between compression stages to increase efficiency.
- Aftercooler:
Removes moisture and enhances air quality by further cooling compressed air following the last step of compression.
- Lubrication System:
Reduces wear and friction by lubricating moving components.
- Control System:
Ensures safe and effective operation by monitoring and controlling many factors, including vibration, temperature, and pressure.
Applications of Large Reciprocating Compressors: Powering Industrial Processes
Because large reciprocating compressors can supply high-pressure air, they are used in a variety of sectors.
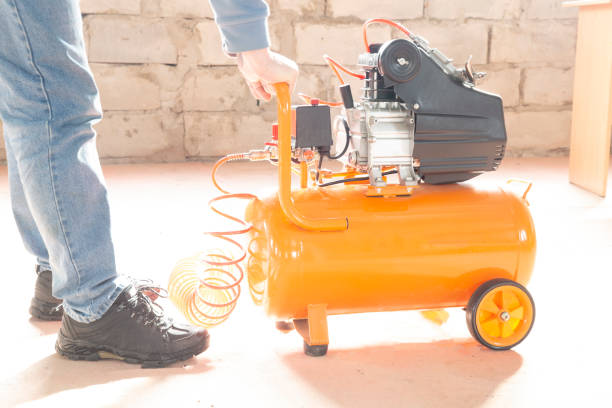
- Oil and Gas Industry:
They are utilized in several processes in oil refineries, including hydrocracking, fluid cracking, and the processing of natural gas.
- Chemical Industry:
The production of chemicals such as ethylene, methanol, and ammonia depend on the supply of high-pressure air from massive reciprocating compressors.
- Petrochemical Industry:
The manufacturing of plastics, synthetic fibers, and other petrochemical goods depends heavily on these compressors.
- Power Generation:
Plant instruments and turbines are powered by compressed air from sizable reciprocating compressors.
- Transmission of Natural Gas:
These compressors are used by large pipelines that carry natural gas over long distances to keep the network’s pressure constant.
- Air Separation Units:
Huge reciprocating compressors are used in the air separation procedures that produce industrial gases such as nitrogen, argon, and oxygen.
Maintaining Peak Performance: Service and Maintenance Practices for Large Reciprocating Compressors
These lifetime and dependability depend heavily on routine servicing and maintenance. Here are some essential guidelines to remember:
- Planned Maintenance plan:
For maintenance procedures including oil changes, filter replacements, and component checks, adhere to the manufacturer’s suggested plan.
- Lubrication:
To reduce wear and friction, proper lubrication is essential. Follow the lubrication intervals and use the lubricants that are indicated.
- Upkeep of the Cooling System:
Maintaining the cooling system on a regular basis will provide ideal heat dissipation and guard against overheating.
- Maintenance of Valve:
To guarantee adequate sealing and stop air leaks, inspect and service valves regularly.
- Packing and Seal Replacement:
Inefficient operation might result from worn valve seals, rod packing, and piston rings. As recommended by the manufacturer, or as part of routine maintenance, replace them as needed.
- Monitoring Vibration:
High vibration may be a sign of impending issues. Put in place programs for monitoring vibration and take quick action to resolve any alarming problems.
- Recordkeeping:
For the sake of future reference and troubleshooting, keep thorough records of all service and maintenance operations.
Repairing Large Reciprocating Compressors: When Expertise Matters
These compressors run at elevated temperatures and pressures. The expertise and experience of qualified technicians enable them to manage repairs securely, reducing the possibility of mishaps or injuries.
- Specialized Tools and Equipment:
Most maintenance staff do not always have access to the specialized tools and equipment needed to repair big reciprocating compressors. Skilled technicians possess the equipment needed to perform precise and timely repairs.
- Troubleshooting Expertise:
It takes skill and experience to identify the underlying cause of an issue in a complicated system such as a big reciprocating compressor. Skilled experts can locate problems quickly and suggest the best course of action.
- Considerations for Warranties:
Manufacturer warranties may be voided by incorrect repairs. Repairs that are made according to manufacturer specifications and preserve warranty coverage are guaranteed when using authorized service providers.
Large Reciprocating Compressors’ Advantages: Efficiently Powering Industry
These reciprocating compressors are the engine of many industrial uses. Here’s why they continue to be a powerful force:
- High Pressure Output:
They can handle tough jobs in the chemical, power generating, and oil and gas sectors by delivering strong compressed air.
- Dependable Performance:
These compressors, which are designed for continuous operation, provide dependable performance you can trust.
- Proven Technology:
Large reciprocating compressors are a safe and well-understood option, with a long history of dependable service and mature technology.
- Scalability:
They may be customized to match the precise airflow (CFM) and pressure (PSI) needs of your application. They come in a range of sizes and combinations.
- Ease of Maintenance:
Regular maintenance procedures guarantee dependable performance and increase these compressors’ longevity.
Conclusion:
Large reciprocating compressors of the highest caliber are available from top manufacturers at LEiYAO Compressors. Discover useful information to maintain the optimal performance of your reciprocating compressors by exploring our website and finding the ideal fit for your industrial demands. You can also look through replacement parts and servicing choices.