Unleash Clean Air Power: A Guide to Diaphragm type Compressor
A Complete Guide to Diaphragm Compressors: The Hero of Gas Compression
Diaphragm type compressor, often referred to as membrane compressors or positive displacement compressors, are essential to many industrial operations. They are excellent in efficiently and cleanly raising the pressure of different gases. Even though they are essential, these workhorses are frequently overlooked. This in-depth manual explores the realm of diaphragm compressors, including their benefits over other compressor technologies, applications, maintenance procedures, and functioning principles.
A Closer Look at Diaphragm Compressors: Positive Displacement vs. Dynamic Compression
Positive displacement compressors are the group that includes diaphragm compressors. Positive displacement compressors trap a certain volume of gas and physically limit its space, increasing pressure, in contrast to dynamic compressors, which employ revolving impellers to accelerate gas and convert kinetic energy into pressure.
The Heart of the Machine: The Diaphragm
The diaphragm is the main part of a diaphragm type compressor. This flexible membrane serves as a barrier between the gas and the driving mechanism. It is usually composed of reinforced textiles or elastomeric materials like PTFE (Teflon). By taking in gas at low pressure during the expansion phase and compressing it when the volume decreases, the diaphragm’s back-and-forth motion generates a variable volume chamber.
Diaphragm compressor types include:
Diaphragm compressors are available in a variety of configurations to meet different needs:
- Mechanically Actuated:
The diaphragm movement of these compressors is powered by a crankshaft and connecting rod mechanism. They can withstand high pressure and are appropriate for a variety of industrial applications.
- Electromagnetically Actuated:
The diaphragm of these compressors is moved in a reciprocating motion by use of electromagnets. They are quiet, small, and perfect for applications requiring little pressure.
- Hydraulically Actuated:
The diaphragm in these compressors is driven by hydraulic pressure, providing accurate control and appropriateness for handling corrosive or hazardous gases.
How Does a Diaphragm Compressor Work?
Within a single cycle, the diaphragm compressor’s operating principle may be divided into four stages:
- Intake:
The diaphragm expands outward, expanding the compression chamber’s capacity. By doing so, a low-pressure area is created, allowing gas to enter via the input valve.
- Compression:
The diaphragm moves inwards and in the opposite direction, decreasing the capacity of the chamber. The check valve on the discharge side closes the trapped gas’s escape path, compressing the gas.
- Discharge:
The check valve opens to let the compressed gas escape when the pressure within the chamber reaches the discharge pressure.
- Repetition:
To provide the required pressure output, the diaphragm keeps up its reciprocating motion and repeats the intake, compression, and discharge cycles.
Diaphragm Compressor Applications: A Versatile Workhorse
Many sectors use diaphragm compressors applications because of their oil-free construction, clean operation, and versatility in handling gases.
- Food and Beverage Processing:
Food and beverage processing include air purging to avoid oxidation, pneumatic ingredient conveyance, and the transfer and aeration of CO2 for carbonation.
- Chemical Processing:
Chemical processing includes pneumatic instrumentation control, metering and dispensing chemicals, and transferring dangerous or corrosive gases.
- Pharmaceutical and medical:
Providing sterile air for medication delivery systems, medical equipment, and laboratory sample processing.
- Environmental Technology:
Environmental technology includes aeration in wastewater treatment, emissions control systems for industrial operations, and air sampling for pollution monitoring.
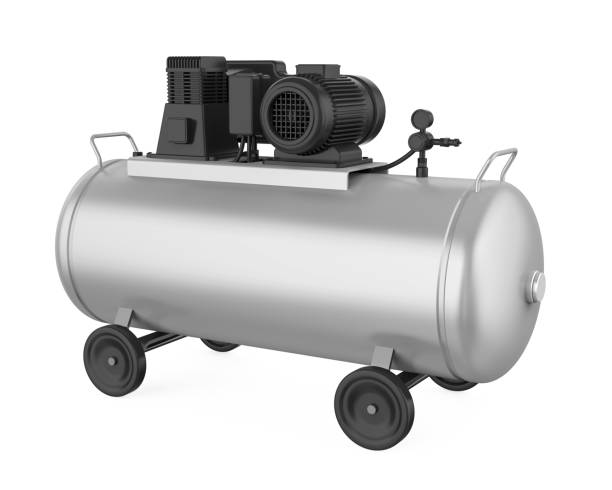
The Advantages of Diaphragm Compressors:
Compared to alternative compressor technologies, diaphragm compressors have the following advantages:
- Oil-Free Operation:
They are perfect for applications needing clean air or delicate procedures since they remove the possibility of oil contamination in the compressed gas.
- Versatility:
Depending on the diaphragm material choice, they can handle a wide range of gases, including corrosive, poisonous, and sterile media.
- Low Maintenance:
The few moving components and straightforward design reduce the need for maintenance.
Silent Operation: When compared to other compressor types, diaphragm compressors usually produce less noise.
- Precise Control:
They are appropriate for delicate applications as they provide good control over pressure and flow rate.
- Compact Design:
A lot of diaphragm compressors are lightweight and small, making it simple to integrate them into current systems.
Diaphragm Compressor Maintenance Guide: Keeping Your Workhorse Running Smoothly
Diaphragm type compressor is dependable workhorses in many different sectors because of their adaptability and oil-free operation. But just as with any gear, regular maintenance is essential to guaranteeing peak performance and extending their life. Here is a thorough diaphragm compressor maintenance guide to help you maintain the optimal operation of your compressor:
Scheduled Inspections:
- Visual Inspection:
Look for wear, fractures, or rips in the diaphragm on a regular basis. Inspect it for any physical impairments or distortions that might affect its capacity to seal. Diaphragm problems may be identified early on to avoid expensive downtime and possible system breakdowns.
- Filter Maintenance:
As directed by the manufacturer, check and replace air intake filters. Filters that are clogged can impede airflow, which lowers compressor performance and may result in overheating.
- Valve Inspection:
Verify that the discharge and intake valves are operating correctly. Keep an ear out for odd sounds that might point to leaks or worn-out valves. Depending on the particular use and the manufacturer’s instructions, certain valves may need to be cleaned or replaced.
- Tightening Fasteners:
Vibrations have the potential to gradually loosen bolts and connections. To maintain ideal system integrity and stop possible leaks, routinely inspect and tighten any loose fasteners.
Cleaning:
- Diaphragm Cleaning:
The type of gas being compressed and the working conditions determine how often the diaphragm has to be cleaned. In clean air applications, a gentle cloth and occasional cleaning may be sufficient. However, more regular cleaning may be required for procedures requiring polluted or dusty surroundings. For information on the right cleaning technique and schedule for your particular diaphragm material and use, refer to the manufacturer’s instructions.
- Inlet and Discharge Ports:
Periodically clean the inlet and discharge ports to get rid of any dust or debris buildup that can obstruct efficient airflow and lower compressor efficiency.
Replacement:
- Diaphragm Replacement:
To preserve compressor performance and avert possible failures, replace the diaphragm as soon as examinations show noticeable wear, cracks, or rips in it. Selecting a new diaphragm that is suitable with the compressed gas and especially made for your compressor model is essential.
- Filters and Valves:
Change worn-out valves and air intake filters in accordance with manufacturer recommendations or when examinations show that they should be replaced.
Conclusion:
These diaphragm type compressor maintenance procedures can help you keep your dependable workhorse running smoothly and performing at its best for many years to come. Visit LEiYAO Compressors for a large assortment of premium diaphragm compressors, replacement parts, and professional assistance.