Methane Compressor: Types, Applications, and Efficiency
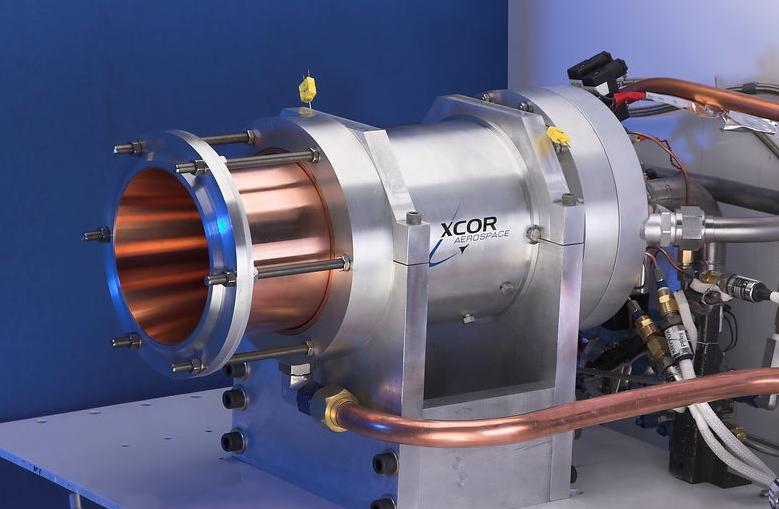
Introduction
Methane Compressor, a primary component of natural gas, plays a vital role in meeting our energy needs while also contributing to environmental sustainability. Efficient methane handling, which includes compression, is crucial for various industries and applications. In this comprehensive guide, we will delve into the world of methane compressors, exploring their types, applications, efficiency considerations, maintenance, safety measures, and future trends.
Definition and Importance of Methane Compression
Methane compression involves the increase in pressure of methane gas, making it suitable for various applications. It is a critical process in the energy sector, environmental applications, and more. Compression ensures that methane can be transported, stored, and utilized efficiently.
Significance of Efficient Methane Handling
Efficient methane handling is essential for several reasons. Firstly, it maximizes the energy output from methane, making it a cost-effective and clean energy source. Secondly, it reduces methane emissions, contributing to environmental goals by curbing greenhouse gas emissions.
Purpose and Scope of the Guide
This guide aims to provide a comprehensive understanding of methane compressors, from their types to their applications and maintenance. Whether you are involved in the energy industry or interested in environmental applications, this guide will equip you with the knowledge you need to make informed decisions.
Types of Methane Compressors
Methane compressors come in various types, each with its unique working principles, advantages, and applications. Let’s explore these types in detail.
Reciprocating Methane Compressors
Working Principle
Reciprocating compressors use a piston-cylinder arrangement to compress methane gas. As the piston moves back and forth, it compresses the gas in the cylinder, increasing its pressure.
Advantages
- High efficiency in low to medium flow rate applications.
- Suitable for intermittent use.
- Can handle high-pressure ratios.
Applications
Reciprocating compressors find use in natural gas processing plants, gas transmission, and storage facilities.
Rotary Screw Methane Compressors
Working Principle
Rotary screw compressors utilize two interlocking helical rotors to compress methane gas. As the rotors turn, they trap and compress the gas between them.
Advantages
- Continuous operation with minimal pulsation.
- Well-suited for medium to high flow rates.
- Relatively low maintenance requirements.
Applications
These compressors are commonly used in natural gas distribution and industrial applications.
Centrifugal Methane Compressors
Working Principle
Centrifugal compressors use a high-speed rotating impeller to accelerate methane gas and then a diffuser to convert the kinetic energy into pressure.
Advantages
- High efficiency in high flow rate applications.
- Compact and lightweight design.
- Low maintenance compared to reciprocating compressors.
Applications
Centrifugal compressors are used in large-scale natural gas liquefaction plants and gas transmission systems.
Applications of Methane Compression
Methane compression plays a pivotal role in various sectors. Let’s explore its applications in detail.
Energy Sector
Methane as a Clean Energy Source
Methane, when burned, produces energy with fewer emissions compared to other fossil fuels. It is a valuable resource for generating electricity and powering vehicles.
Methane Storage and Distribution
Efficient compression enables the safe storage and transportation of methane to end-users, including power plants and industrial facilities.
Natural Gas Processing Plants
Compression is a fundamental step in processing raw natural gas, making it suitable for distribution and consumption.
Environmental and Biogas Applications
Landfill Gas Recovery
Methane generated in landfills can be captured and compressed for energy generation, reducing methane emissions and harnessing a renewable energy source.
Biogas Production
Biogas, a methane-rich gas produced from organic matter, can be compressed for use in various applications, including heating, electricity generation, and vehicle fuel.
Emission Reduction
Compression of methane from various sources, including agriculture and wastewater treatment, aids in reducing methane emissions, mitigating its impact on climate change.
Factors to Consider When Choosing a Methane Compressor
Selecting the right methane compressor is crucial for optimal performance and efficiency. Consider the following factors:
Capacity and Flow Rate Requirements
Determine the volume of methane you need to compress and the required flow rate. Matching the compressor’s capacity to your needs is essential for efficiency.
Energy Efficiency and Environmental Considerations
Choose a compressor with high energy efficiency to minimize operational costs and reduce carbon footprint. Look for technologies that reduce methane leakage.
Safety Features
Ensure the compressor has safety features such as pressure relief valves and automatic shutdown systems to prevent accidents.
Maintenance and Serviceability
Consider the ease of maintenance and availability of spare parts when choosing a compressor. Regular maintenance is essential for long-term reliability.
Maintenance and Care of Methane Compressors
Regular maintenance is vital to ensure the longevity and optimal performance of methane compressors. Here are some important considerations:
Importance of Regular Maintenance
Scheduled maintenance helps prevent breakdowns, extends the compressor’s lifespan, and ensures safe operation.
Recommended Maintenance Tasks and Schedules
Follow manufacturer-recommended maintenance tasks and schedules, including lubrication, inspection, and parts replacement.
Tips for Ensuring Longevity and Optimal Performance
Implement best practices such as monitoring performance parameters, maintaining proper ventilation, and addressing issues promptly to maximize compressor lifespan.
Methane Compressor Safety Measures
Safety is paramount when handling methane gas. Implement the following safety measures to prevent accidents:
Safety Precautions for Handling Methane Gas
Train personnel on safe handling procedures, including the use of personal protective equipment and proper ventilation in confined spaces.
Ventilation and Gas Detection
Maintain adequate ventilation in compressor areas and install gas detection systems to monitor methane levels and trigger alarms if necessary.
Emergency Procedures and Training
Develop and communicate emergency procedures, including evacuation plans and response protocols, and ensure that personnel are trained in their implementation.
Future Trends in Methane Compressor Technology
The field of methane compression continues to evolve, driven by the need for greater efficiency and sustainability. Here are some future trends to watch out for:
Advancements in Efficiency and Energy Savings
Ongoing research and development aim to improve compressor efficiency, reduce energy consumption, and minimize methane leakage.
Smart Monitoring Systems for Improved Performance
The integration of advanced monitoring and control systems will enable real-time performance optimization, predictive maintenance, and energy savings.
Sustainable Practices in Methane Compression
The industry is increasingly focusing on sustainable practices, including the use of renewable energy sources for compression and reducing methane emissions throughout the process.
Conclusion
In conclusion, methane compression is a critical process with far-reaching applications in the energy sector and environmental sustainability. Efficient methane handling through the use of appropriate compressors is essential for harnessing its potential while minimizing its impact on the environment. We encourage the adoption of efficient methane handling technologies to meet our energy needs while safeguarding our planet for future generations. Whether you are involved in the energy industry or environmental initiatives, understanding methane compression is a valuable step towards a cleaner and more sustainable future.