Powering Up: High-Pressure Piston Compressors
High-pressure piston compressors, vital in numerous industries, are mechanical devices designed to elevate gas pressure for diverse applications. These workhorses play a pivotal role in powering manufacturing processes, facilitating energy storage, and supporting vital operations across sectors.What are High-Pressure Piston Compressors?
How high-pressure piston compressors work
High-pressure piston compressors operate on the principle of reciprocating motion. They use pistons within cylinders to compress the gas, creating high-pressure conditions. During the compression cycle, gas is drawn into the cylinder, compressed, and then expelled at elevated pressure, providing a versatile source of high-pressure gas.
Components and key elements
- Pistons and cylinders: Pistons move within cylinders to create compression. Their size and design dictate the compressor’s capacity and pressure output.
- Valves: Valves ensure one-way gas flow, allowing gas to enter the cylinder during the intake stroke and exit at high pressure during the compression stroke.
- Lubrication systems: Lubrication is essential to reduce friction and wear in piston compressors. Depending on the type, they may employ oil lubrication or be oil-free, each with distinct advantages.
Different types and configurations
- Single-stage and multi-stage: Single-stage compressors compress gas in a single step, while multi-stage compressors use multiple cylinders to achieve higher pressures. Multi-stage compressors are preferred for extremely high-pressure applications.
- Oil-lubricated and oil-free: Oil-lubricated compressors use oil for piston lubrication but may require oil separation in the discharge. Oil-free compressors eliminate the need for oil, making them suitable for applications where oil contamination is a concern.
Applications across industries
- Manufacturing: Used for powering pneumatic tools, providing compressed air for production lines, and controlling various industrial processes.
- Oil and gas: Essential for gas compression, transportation, and storage in the oil and gas industry, including natural gas pipelines and gas injection processes.
- Food processing: Employed for packaging, food preservation, and maintaining sanitary conditions by providing compressed air for conveyor systems and equipment.
- Pharmaceuticals: Used in critical applications such as pharmaceutical packaging and sterilization processes, where high-pressure, contaminant-free air is vital for product quality and safety.
Benefits and Advantages
Precision Pressure Control
High-pressure piston compressors excel at generating and maintaining elevated gas pressures, making them the go-to choice for applications that require meticulous pressure regulation. They consistently deliver compressed gas at industry-specific levels, ensuring dependable performance.
Energy Efficiency
Engineered with a focus on energy efficiency, these compressors optimize the compression process to minimize power consumption. Features like variable speed drives and efficient components contribute to substantial energy savings, establishing their cost-effectiveness in the long term.
Robust Reliability
High-pressure piston compressors are renowned for their rugged construction and durability. They are purpose-built to endure challenging operating conditions, offering extended service lives with minimal maintenance requirements. Their unwavering reliability minimizes downtime, particularly in critical applications.
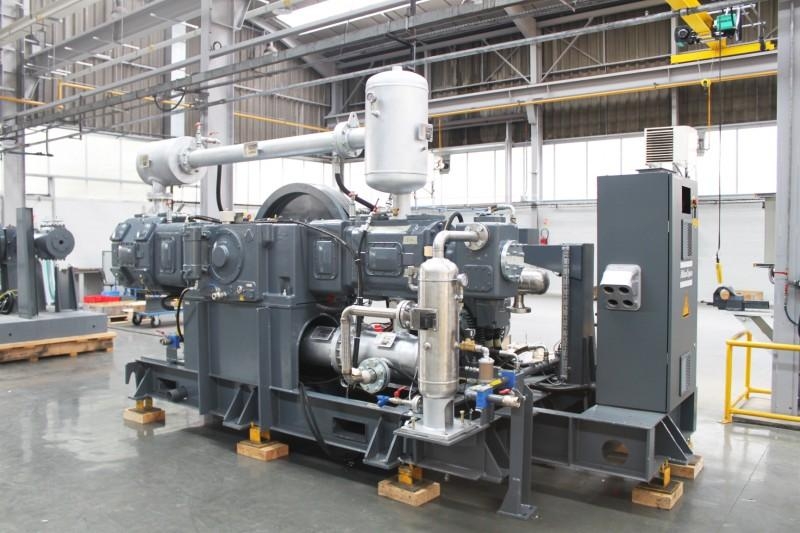
Economic Viability
While their initial upfront cost might surpass that of some alternative compressor types, high-pressure piston compressors prove economically sound over their operational lifespan. Their efficiency, longevity, and low maintenance demands translate into long-term cost savings. Additionally, reduced energy consumption further bolsters their cost-effectiveness.
Environmental Friendliness
Particularly noteworthy are oil-free high-pressure piston compressors, which eliminate the risk of oil contamination in compressed air. This makes them particularly suitable for industries subject to stringent environmental regulations. Moreover, their energy-efficient design contributes to reduced greenhouse gas emissions linked to energy generation.
Maintenance and Care
Regular Inspection and Preventive Maintenance
Regular inspection schedules and proactive maintenance routines are essential to keep high-pressure piston compressors in peak condition. This includes checking for wear and tear, inspecting seals, valves, and lubrication systems, and addressing potential issues before they become critical.
Common Issues and Troubleshooting
Familiarity with common problems like leaks, valve malfunctions, or overheating is crucial for timely troubleshooting. Comprehensive troubleshooting procedures help diagnose issues promptly, preventing costly downtime.
Lubrication and Cooling System Maintenance
Proper lubrication is vital for reducing friction and extending the compressor’s lifespan. Lubrication systems should be regularly checked, and oil levels maintained as needed. Cooling systems should also be monitored to prevent overheating.
Extending the Lifespan of High-Pressure Piston Compressors
Maximizing the life of these compressors involves meticulous care. This includes using high-quality lubricants, following manufacturer-recommended maintenance schedules, monitoring performance parameters, and implementing energy-efficient practices. Regularly assessing the compressor’s condition and addressing issues promptly will help extend its operational lifespan, providing a solid return on investment.
Future Trends and Innovations of High-Pressure Piston Compressors
Emerging Technologies in High-Pressure Piston Compressors
Advancements in materials science are leading to lighter, stronger compressor components. Integration of IoT (Internet of Things) enables real-time monitoring, predictive maintenance, and enhanced performance optimization. Furthermore, magnetic bearings and variable speed drives offer efficiency improvements and operational flexibility.
Industry Outlook and Predictions
The demand for high-pressure piston compressors is set to rise, driven by expanding industrial sectors and stringent environmental regulations. Manufacturers are focusing on modular, scalable designs to cater to diverse applications. With industries moving towards Industry 4.0, the integration of AI and advanced analytics in compressors will become commonplace, ensuring optimal operations and minimized downtimes.
CONCLUSION
High-pressure piston compressors stand as a testament to the evolving synergy between technology and industry needs. As we pivot towards a future that emphasizes efficiency and sustainability, these compressors are embracing innovations, from advanced materials to IoT integrations. The integration of green solutions not only underscores the industry’s commitment to environmental stewardship but also reflects its adaptability to emerging global demands. As these machines power up to meet tomorrow’s challenges, their continuous evolution is an inspiring journey of adapting, innovating, and transcending boundaries. The future holds promise for these powerhouses, paving the way for smarter, greener, and more efficient industrial processes.