Compressor factory
A compressor factory is an industrial facility where compressors are manufactured. Compressors are mechanical devices used to increase the pressure of various gases or air, and they find applications in numerous industries, from refrigeration and air conditioning to the oil and gas sector. Key aspects of a compressor factory include:
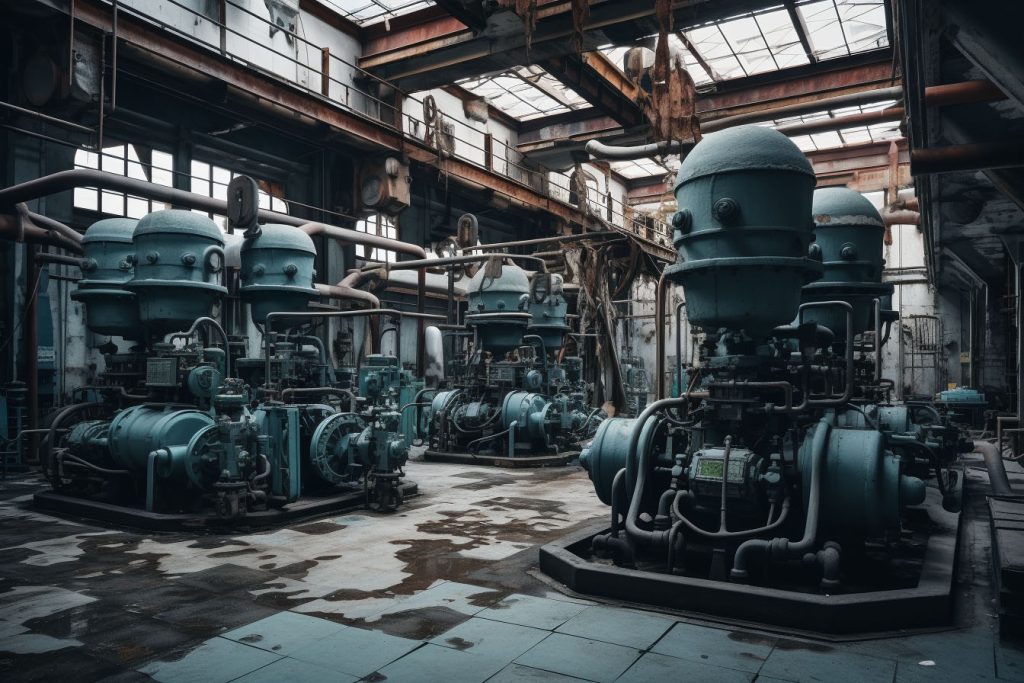
- Manufacturing Areas: These include production lines where different types of compressors (like reciprocating, rotary screw, centrifugal, and diaphragm compressors) are assembled. Each line may be specialized for a particular type or size of compressor.
- Quality Control and Testing: A critical part of the manufacturing process is rigorous testing to ensure that each compressor meets industry standards and specifications. This could involve pressure tests, leak tests, and performance evaluations.
- Research and Development (R&D) Department: To stay competitive, a compressor factory often has an R&D department focused on developing new technologies, improving efficiency, and reducing costs.
- Supply Chain and Logistics: The factory would have a robust supply chain system to manage the inflow of raw materials (like metals, plastics, and electronic components) and the distribution of finished compressors to customers.
- Safety Protocols: Due to the nature of the work, which may involve handling high-pressure systems and heavy machinery, safety is a top priority in a compressor factory. This includes training for employees and adherence to industry safety standards.
- Environmental Considerations: Modern compressor factories often incorporate environmentally friendly practices, such as energy-efficient manufacturing processes and waste reduction measures.
- Workforce: A mix of skilled labor, engineers, quality control specialists, and other professionals are essential for the smooth operation of the factory.
- Customer Support and Service Centers: Many compressor factories also have dedicated teams for customer support and service, providing maintenance and repair services for their products.
- Automation and Technological Integration: With the advancement of technology, many compressor factories now incorporate automation and IoT (Internet of Things) solutions for enhanced production efficiency and real-time monitoring of the manufacturing process.
Types of compressors
In your outline about compressor types, you’ve covered the main categories of compressors used in various industries. Let’s delve a bit deeper into each type:
Reciprocating Compressors
These are positive displacement machines where the compressing and displacing element is a piston having a reciprocating motion within a cylinder. They can be further divided into:
- Single-Acting: Compresses air on only one side of the piston.
- Double-Acting: Compresses air on both sides of the piston, increasing efficiency.
Rotary Compressors
These compressors use rotors to compress the air. They include:
- Screw Compressors: Utilize two meshing helical screws, known as rotors, to compress the air.
- Vane Compressors: Consist of a slotted rotor with varied blade placement, which guides air into a chamber and compresses the volume.
- Scroll Compressors: Involve two spiral elements; one stationary and one moving in small eccentric circles inside the other, trapping and compressing pockets of air.
Centrifugal Compressors
These are dynamic compressors where compression is achieved through the conversion of angular momentum imparted by a rotating impeller. Types include:
- Radial Compressors: Air flows radially and is compressed by the centrifugal force generated by the rotating impeller.
- Axial Compressors: Air moves parallel to the axis of rotation. They have high flow rates and are used in large applications like jet engines.
Compressor Components
Compressor Motor
This is the driving force of a compressor, converting electrical or fuel energy into mechanical energy to drive the compressor mechanism. There are two primary types:
- Electric Motor: These are the most common in industrial and residential applications. They convert electrical energy into mechanical energy. Electric motors are preferred due to their efficiency, low maintenance, and because they don’t produce exhaust gases.
- Gas Engine: Used primarily in situations where electricity is not available or in portable compressors. Gas engines are internal combustion engines that burn fuel to generate mechanical energy. They are ideal for remote construction sites or mobile applications but require more maintenance and produce exhaust gases.
Compressor Controls
These components are essential for managing the operation of the compressor, ensuring efficiency, and preventing damage.
- Pressure Switches: These are critical for controlling the start and stop of the compressor motor based on the air pressure in the tank. When the pressure drops below a certain preset level, the pressure switch activates the motor to refill the tank. Conversely, when the maximum pressure is reached, the switch turns off the motor to prevent over-pressurization.
Additional controls often found in compressors include:
- Thermostats and Temperature Controls: To monitor and regulate the temperature of the compressor, especially in systems where overheating could be a concern.
- Variable Speed Drives (VSD): These are used in advanced compressors to adjust the motor speed based on demand, thereby improving efficiency and reducing energy consumption.
- Safety Valves: Automatically release air if the pressure exceeds safe levels, preventing equipment damage or accidents.
Applications of compressors
Compressors have a wide range of applications across various industries, each leveraging the unique capabilities of compressed air or gas for different purposes. Let’s explore these applications in more detail:
Industrial Applications
Compressors in the industrial sector are critical for numerous processes:
- Manufacturing: In manufacturing plants, compressors are used for powering pneumatic tools, automation systems, and process control operations. They are essential in sectors like automotive manufacturing, where they operate machinery for assembling parts and spray painting.
- Aerospace: The aerospace industry relies heavily on compressors for various applications, including air supply for wind tunnels, pneumatic systems maintenance in aircraft, and even in the manufacturing processes for aircraft components.
Commercial Applications
In the commercial sector, compressors are used in systems that affect our everyday environments:
- HVAC Systems: Heating, Ventilation, and Air Conditioning (HVAC) systems use compressors to circulate refrigerant and control the temperature in commercial buildings, offices, shopping malls, and other public spaces.
- Refrigeration: Commercial refrigeration systems, like those in supermarkets and food storage facilities, depend on compressors to maintain the low temperatures needed for preserving perishable goods.
Automotive Applications
Compressors also play a crucial role in the automotive industry:
- Air Conditioning: Compressors are at the heart of a car’s air conditioning system, compressing the refrigerant and circulating it through the system to cool the interior of the vehicle.
- Engine Turbocharging: Turbochargers use compressors to force more air into the combustion chamber of an engine, increasing power and efficiency. This technology is widely used in both performance and standard passenger vehicles to improve engine output and fuel efficiency.