3 Stage Reciprocating Compressors: Power & Efficiency for Your Industry
Understanding the 3 Stage Reciprocating Compressor:
A positive displacement mechanism is employed by a 3 stage reciprocating compressor, which is often referred to as a multi-stage air compressor, to attain extraordinarily high-pressure air output. This is an overview of its features:
- Core mechanism:
The compressor’s core mechanism consists of a piston contained in a cylinder. The piston increases the pressure in the cylinder by compressing the air as the crankshaft turns.
- The Influence of Phases:
Three distinct phases of compression are included in a three-stage design, in contrast to single-stage compressors. There are intervals of intercooling between the phases of air compression. By dispersing the heat produced during compression, these intercoolers reduce temperatures and increase efficiency.
- The Upshot:
A three-stage reciprocating compressor produces noticeably greater discharge pressures than single-stage versions because it achieves compression in phases.
The Comparison Arena: 3-Stage vs. Its Competitors
Even though three-stage reciprocating compressors are superior in certain situations, it’s important to comprehend their benefits in comparison to alternative solutions:
Three-Stage vs One-Stage:
Compressors with one stage have a less complicated design and a cheaper starting price. They could be less effective in high-pressure applications, nevertheless, because of their restricted pressure output.
3-Stage vs. 2-step:
Because 3-stage compressors include an extra intercooling step, they can generate even higher pressure outputs while still operating more efficiently than 2-stage compressors.
Inquiring Minds Want to Know: Information Needs Addressed
When thinking about a 3 stage reciprocating compressor, there are a few important things to consider. This handbook offers responses to some of the most frequently asked questions:
- Working Principle:
Earlier in the article, a thorough description of the three steps of the compression process and the function of intercooling was given.
- Maintenance:
For optimum performance and longevity, regular maintenance procedures such as air filter replacements, oil changes, and condensate draining are essential. Please see the manufacturer’s instructions for details on particular maintenance regimens.
- Cost:
Compared to single-stage devices, the initial cost of a 3 stage reciprocating compressor may be greater. However, over time, things like dependability, low maintenance requirements, and energy efficiency can result in considerable cost savings.
- Manufacturers:
Three stage reciprocating compressors are available from several manufacturers. It is advised to carry out in-depth investigations to find brands that are renowned for dependability and quality. We are pleased to present a wide range of 3 stage reciprocating compressors from top manufacturers here on our website.
Performance Benefits: Why Choose a 3-Stage Reciprocating Compressor?
The remarkable performance of 3-stage reciprocating variants makes them stand out among other industrial air compressors. Here’s a closer look at the main advantages that make them an appealing option for several applications:
- High-Performance Function:
The multi-stage design is what makes it magical. In contrast to single-stage compressors, which compress air all at once, three-stage models do so gradually. Three stages of air compression are used, with intercoolers positioned thoughtfully in between. These intercoolers remove heat produced during compression by functioning similarly to radiators.
Reduced energy consumption: Compared to using less efficient compressor types, you’ll pay less in electricity.
Reduced wear and tear: Longer compressor lifespans and lower maintenance costs are the results of cooler working temperatures, which also reduce stress on interior components.
Environmentally friendly: 3-stage compressors are a more sustainable option since they use less energy, which reduces their carbon impact.
- Low-Maintenance Needs:
Reciprocating compressors with three stages are renowned for their dependability and easily manageable maintenance needs. The following factors add to their minimal maintenance requirements:
Simple and Robust Design: The basic mechanism is based on the proven technology of a piston and cylinder, which has few moving parts. As a result, fewer parts can break easily.
Decreased Wear from Cooler Operation: The intercooling procedure, as previously indicated, reduces heat-related stress on internal components, which results in a reduction in wear and tear.
Simple Maintenance Access: The majority of three-stage reciprocating compressors are built with easily navigable access points for standard maintenance procedures such as air filter replacements and oil changes.
- Reliable Air Delivery:
A reciprocating compressor may be your trustworthy ally when your activities depend on a steady supply of compressed air. This is the reason why:
Constructed for Continuous Duty: The performance of these compressors is not compromised even under prolonged operation. They are therefore perfect for industrial environments where a steady supply of air is essential.
Sturdy Construction: To guarantee that the compressor can survive harsh industrial settings, manufacturers use premium materials and sturdy construction methods.
Consistent Pressure Output: The multi-stage design with intercoolers guarantees a dependable and constant high-pressure air supply, which is essential for operating a range of industrial equipment and tools.
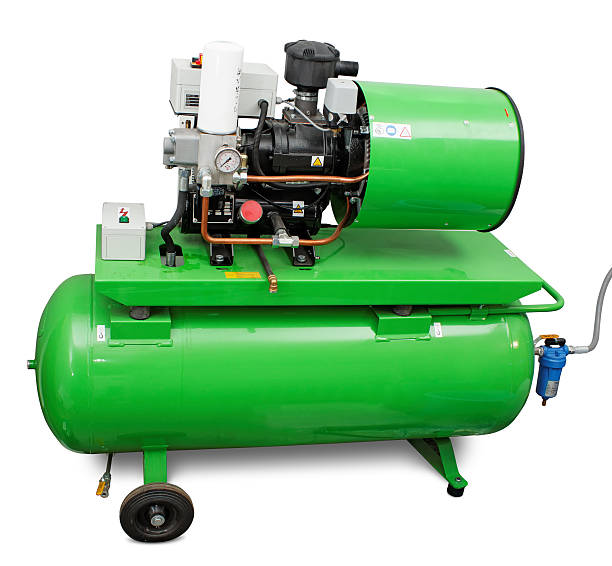
Applications: Where the Power Shines?
Because they can produce high-pressure air, these reciprocating compressors are used in a variety of sectors. Here are a few well-known instances:
- Industrial Air Systems:
These compressors operate machinery in industries such as mining, building, and manufacturing, and they are the lifeblood of many industrial operations.
- High-Pressure Air Generation:
The high-pressure output of three-stage compressors is essential for processes like gas engine starting, plastic injection molding, and sandblasting
- Ongoing Duty Activities:
Because of their sturdy construction, they are perfect for applications that need a consistent supply of compressed air.
Performance Specifications of Reciprocating Compressor:
When deciding whether an industrial air compressor is appropriate for a certain application, its performance characteristics play a critical role. Some important performance requirements to take into account are as follows:
- Cubic Feet per Minute (CFM):
The amount of air that the compressor can produce at a certain pressure is measured in cubic feet per minute, or CFM. Selecting a compressor that can deliver the necessary CFM for the application is crucial.
- Horsepower (HP):
This is a unit of measurement for the compressor motor’s power output. More air can be delivered at a given pressure by a compressor with greater horsepower.
- Maximum Pressure:
This indicates the highest pressure that the compressor is capable of producing. Selecting a compressor that can provide the necessary pressure for the application is essential.
Conclusion:
This article delves deep into the world of 3 stage reciprocating compressor, exploring their functionality, and performance benefits.LEiYAO Compressors, provide our global customers with all-inclusive, one-stop solutions while guaranteeing great product quality and first-rate service.